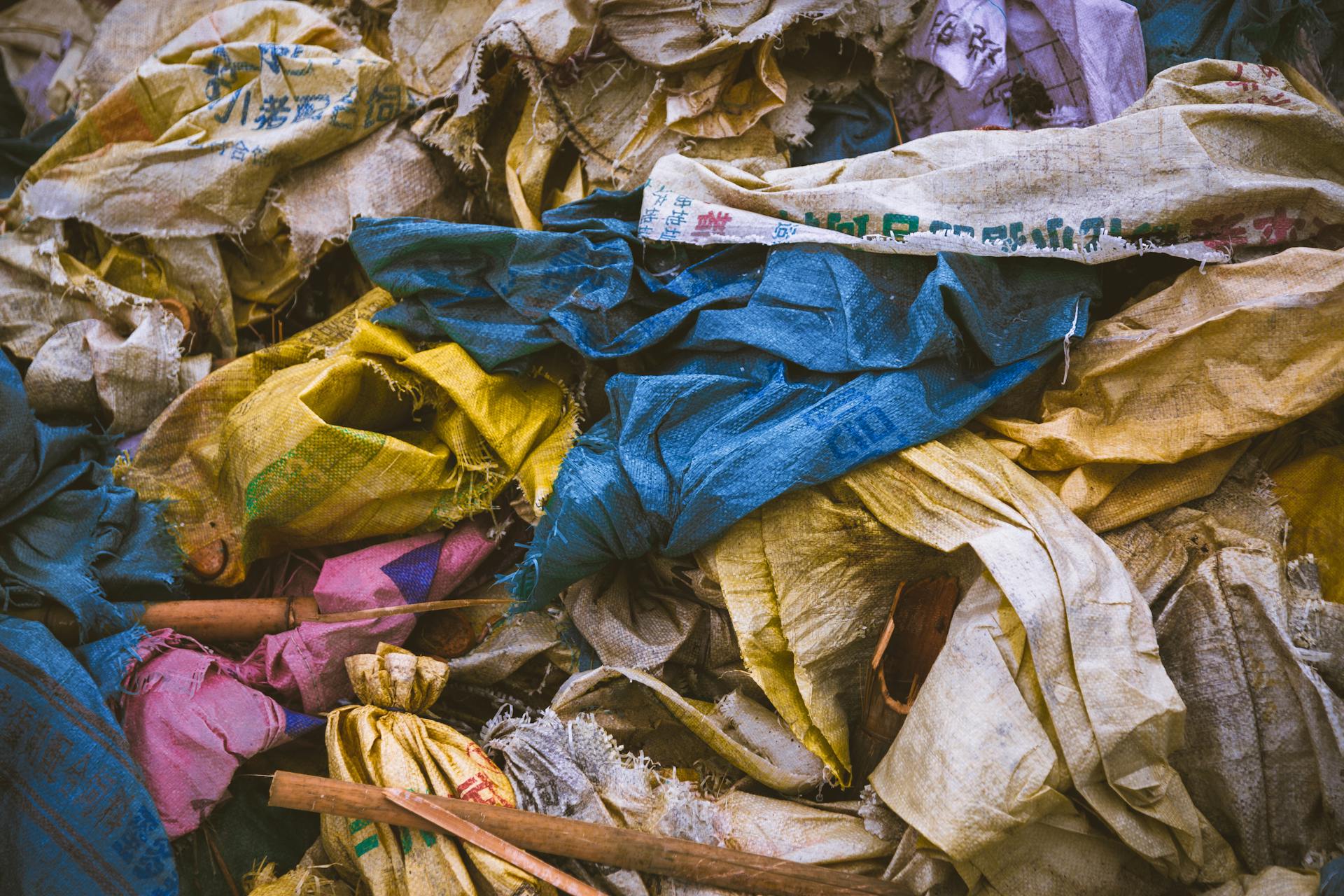
Biaxially Oriented Polypropylene Bags are incredibly versatile and durable. They can be used for packaging a wide range of products, from food and beverages to cosmetics and pharmaceuticals.
One of the key benefits of BOPP bags is their high barrier properties, which prevent the transmission of gases, moisture, and light. This makes them ideal for packaging sensitive products that require protection from the environment.
BOPP bags are also incredibly flexible and can be easily molded into various shapes and sizes to fit specific packaging needs. Their versatility is one of the reasons why they're so widely used in various industries.
Their high tensile strength and resistance to punctures and tears also make them a reliable choice for packaging heavy or fragile items.
What Are PP and OPP Bags?
PP bags are made from a strong and versatile material called polypropylene, which is often used to make coatings, films, tapes, and printed FIBCs on a mass scale.
Polypropylene is a polymer that's resistant to many chemicals and has favorable heat and barrier properties, making it a durable material.
PP bags can be manipulated to produce OPP and BOPP materials, but in their basic form, they're often used for general-purpose packaging.
OPP bags, on the other hand, are a type of polypropylene film that's been stretched in one direction, offering better strength, clarity, and printability compared to PP film.
OPP bags tend to be used for labels and small film bags because of their improved properties.
BOPP bags, which are made from biaxially oriented polypropylene, offer even more strength, printability, and clarity than PP and OPP bags, making them suitable for more demanding applications.
Advantages and Characteristics
BOPP bags are incredibly strong and durable, capable of handling large load capacities with ease. Their exceptional tensile strength and resistance to tears and punctures make them a reliable choice for packaging.
One of the standout features of BOPP bags is their superior dimensional stability and water resistance. This means they can withstand various environmental conditions without compromising their shape or integrity.
BOPP bags also offer superior print quality, allowing for high-quality Flexographic printing up to 10 colors. This makes them ideal for products that require intricate branding and printing details.
Some notable characteristics of BOPP bags include:
- Exceptional tensile strength & durability
- Tear and puncture resistant
- Superior dimensional stability and water resistance
- Superior print quality
- Scratch and rub resistant
- Custom designed to meet client specifications
Advantages/Characteristics
BOPP bags are incredibly durable, with exceptional tensile strength that allows them to carry large loads. They're also tear and puncture resistant, reducing costly losses of products and reworking costs.
One of the standout features of BOPP bags is their superior print quality. They can be printed with high-quality Flexographic printing up to 10 colors, making them perfect for branding and marketing efforts.
BOPP bags are also highly versatile, available in various formats such as heat cut or cold cut, and can be gusseted or pillow/tube. They can even be designed with anti-slip treatment for added convenience.
In terms of functionality, BOPP bags are ideal for automated bagging systems and are widely used for added value or high visibility products. They're also convenient for products that require a handle support option.
Here are some key characteristics of BOPP bags:
BOPP bags are also recyclable, which is a significant advantage in today's eco-conscious world. However, it's worth noting that they're not biodegradable.
Pros and Cons of PP and OPP Bags
PP and OPP bags have their advantages.
PP bags are great for industries that require high moisture resistance, such as the food and pharmaceutical industries. They can withstand high temperatures and are easy to clean.
One of the main cons of PP bags is their high cost. They are also not suitable for industries that require high gas barrier properties.
OPP bags, on the other hand, offer excellent gas barrier properties, making them ideal for industries like food, pharmaceuticals, and pet food. They are also more affordable than PP bags.
However, OPP bags have a lower moisture barrier than PP bags, which can be a drawback in certain applications.
Manufacturing and Materials
The manufacturing process for biaxially oriented polypropylene (BOPP) bags is quite fascinating. Biaxial orientation of the polypropylene film is the first step, which involves stretching the film in both directions to enhance its strength and clarity.
The printing process is where the graphics are added, using specialized inks that ensure the images are vibrant and long-lasting. The film is then laminated onto the woven polypropylene fabric using adhesives.
The final steps involve cutting and stitching the laminated material into the desired sizes to form bags. Each bag undergoes rigorous quality checks to ensure it meets the required standards.
Polypropylene (PP)
Polypropylene (PP) is a versatile thermoplastic polymer that serves as the core material in BOPP bag production. It's a great choice for packaging due to its unique combination of being lightweight while maintaining robustness.
Polypropylene is resistant to water, oils, and most chemicals, ensuring the contents of the bag remain protected.
This material is also recyclable, aligning with sustainable packaging goals.
Here are some key benefits of polypropylene:
- Lightweight and Durable
- Resistance to Moisture and Chemicals
- Recyclable
The biaxial orientation process in BOPP bags stretches the polypropylene film in both the machine direction (MD) and transverse direction (TD), enhancing its strength, clarity, and barrier properties.
Manufacturing Process Overview
The manufacturing process for BOPP bags involves several key steps.
The first step is biaxial orientation of polypropylene film, where the film is stretched in both directions to enhance its strength and clarity. This process is crucial in producing high-quality bags.
Printing is the next step, where high-quality graphics are printed on the film using specialized inks. The printing process allows for vibrant and detailed designs.
Lamination is the process of attaching the printed film to a woven polypropylene fabric using adhesives. This step is essential in creating the durable and long-lasting material used for BOPP bags.
The laminated material is then cut into the desired sizes and stitched to form bags. This step requires precision and attention to detail.
Each bag undergoes rigorous quality checks to ensure it meets the required standards. This quality control process is vital in producing bags that are safe and reliable for use.
Here are the key steps in the manufacturing process:
- Biaxial Orientation of Polypropylene Film
- Printing
- Lamination
- Cutting and Stitching
- Quality Control
Additives for Enhanced Performance
Additives play a crucial role in enhancing the performance of polypropylene bags. They can be tailored to specific applications, ensuring the bags meet the required standards.
Anti-static agents are a type of additive that reduces the accumulation of static electricity, preventing dust and dirt from clinging to the surface. This makes handling and stacking bags much more efficient.
UV stabilizers protect the bags from degradation caused by prolonged exposure to sunlight, making them suitable for outdoor storage and transportation. This is particularly important for bags that will be exposed to direct sunlight for extended periods.
Slip agents are added to reduce the coefficient of friction between the bag surfaces, improving handling and packaging efficiency. This can be seen in factories where bags are constantly being moved and handled.
To produce visually appealing bags, colouring agents and pigments are added. These enable the creation of vibrant, high-quality prints that are crucial for branding and marketing purposes.
Laminates for Protection
Laminating BOPP bags involves bonding a layer of BOPP film to a woven polypropylene fabric.
This process creates a bag that can handle heavier loads.
The combination of the BOPP film and woven fabric provides increased strength.
Laminates also provide a moisture barrier, ensuring that the contents remain dry and intact.
This is especially important for protecting sensitive items from moisture damage.
The lamination process gives the bags a glossy or matte finish, enhancing their visual appeal.
This can be a big plus for companies looking to brand their products with a professional look.
Adhesives for Bonding
Adhesives play a vital role in securing the layers of the bag during the lamination process.
They are specially formulated to ensure strong bonding between the BOPP film and woven fabric, maintaining the integrity of the bag.
High-quality adhesives are designed to withstand environmental conditions, resisting moisture and temperature variations.
This means that the bags will perform well in diverse environments, without compromising their structure or functionality.
Types of OPP Bags
BOPP bags provide high tensile strength, excellent clarity, and a high degree of dimensional stability and flatness. They're a great option for many applications.
BOPP bags have a low electrostatic charge, which can be beneficial in certain industries. This property makes them a good choice for packaging sensitive materials.
Aesthetically, BOPP bags have a high-gloss finish, making them visually appealing. They also offer reverse printing ability, which can be a plus for branding.
BOPP bags are resistant to oils and greases, making them a good option for packaging food products. They're also not affected by moisture, which means they won't wrinkle or shrink with environmental changes.
BOPP bags are recyclable and classified in the No. 5 plastic recycling stream accepted by some recycling facilities. However, they're not biodegradable, which is a drawback.
Salient Features
These bags are incredibly versatile, coming in many different sizes to suit various needs.
They're also water-resistant and moisture-proof, thanks to their laminated properties.
One of the standout features is the option for a gusseted design, which adds extra flexibility.
Double side printing is available, allowing for up to 8 different colours to be used.
These bags are built to last, being durable and tear-resistant, and even seepage-proof.
The stitching is of high quality, using multifilament white or coloured yarn.
You can customize the dimensions, designs, and colours to meet your specific requirements.
And the best part? These bags are 100% environmentally friendly, being fully recyclable.
Frequently Asked Questions
What is the difference between PP bags and Bopp bags?
PP bags are highly durable and suitable for heavy-duty applications, while BOPP bags offer enhanced tear resistance due to the added film. The choice between the two depends on your specific needs and the level of handling your products will receive.
Who uses Bopp bags?
Bopp bags are commonly used in packaging and shipping dry goods, such as building materials, pet food, and agricultural products. They provide a durable and moisture-resistant solution for protecting these items during transportation.
What is a bopp bag?
A BOPP bag is a lightweight, strong storage bag made from biaxially-oriented polypropylene. It's ideal for storing items due to its moisture-resistant properties.
Sources
- https://www.manyan.com/bopp/
- https://sahpolymers.com/manufacturing-of-bopp-bags/
- https://www.firstagroup.com/resources/breaking-down-the-differences-between-pp-opp-and-bopp-bags.html
- https://missisystems.ca/bopp-(biaxially-oriented-polypropylene)-laminated-bags.php
- https://dktechnofab.com/bopp-bags-biaxially-oriented-polypropylene-bags/
Featured Images: pexels.com