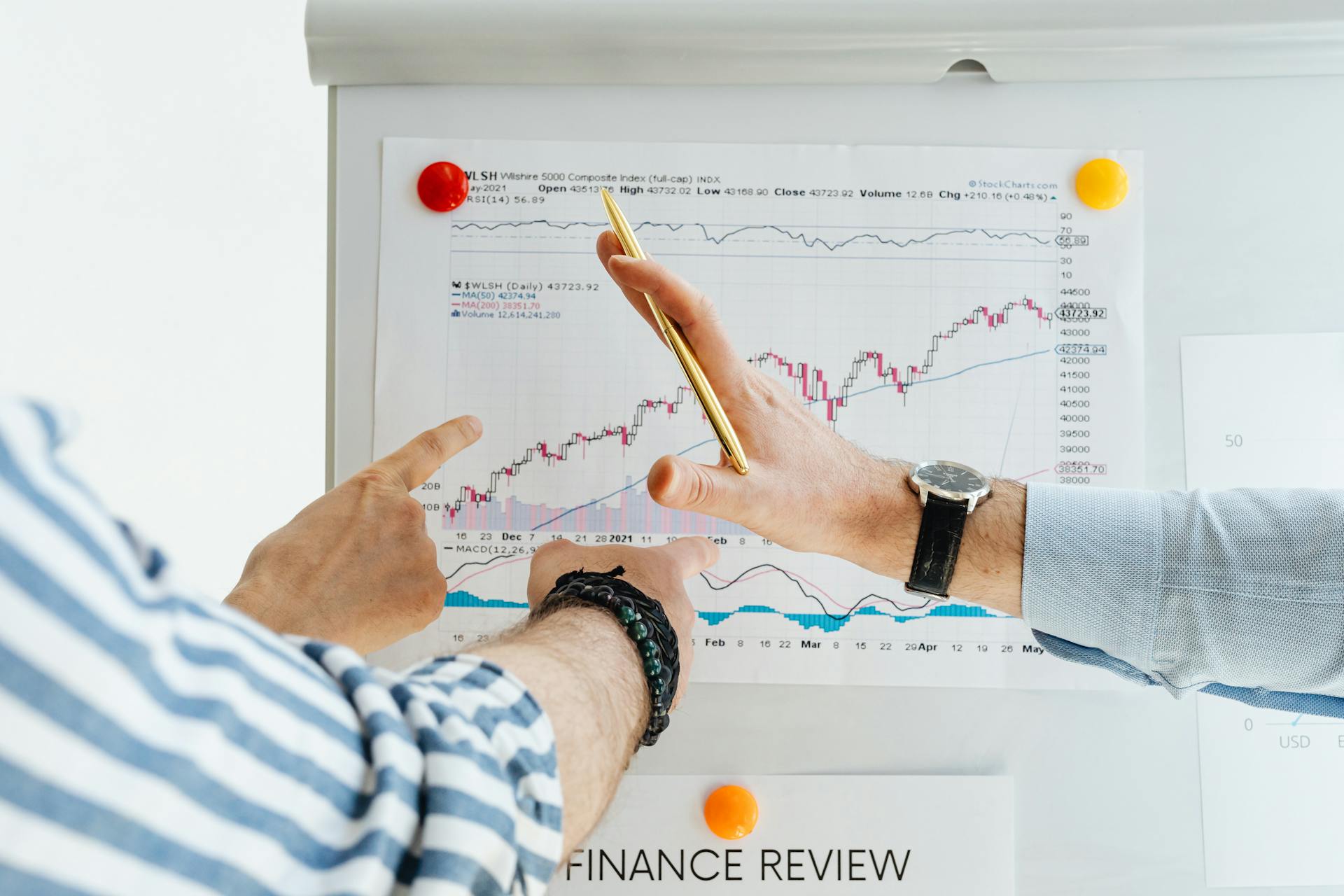
Improving the time between order and delivery can make a huge difference in customer satisfaction and loyalty. A study found that 70% of online shoppers expect delivery within 7-10 business days.
In some cases, delivery times can be as short as 1-3 business days, depending on the shipping method and location. This is often seen in the e-commerce industry where same-day or next-day delivery is a competitive advantage.
However, longer delivery times can be a result of various factors, including the distance between the buyer and seller, the shipping carrier's efficiency, and the seller's inventory management.
You might enjoy: Last Day to Order for Christmas Delivery
Importance of OLT
Calculating the time between order and delivery is crucial for businesses to optimize their operations and reduce costs. OLT (Order-to-Launch Time) formulas help determine this time period.
The OLTRequested formula calculates the time between the customer's wish date and the order entry date. This is the difference between when the customer wants the material and when they place the order.
By optimizing lead time, businesses can reduce their inventory costs. This is because knowing exactly how long it takes between reorders and delivery allows you to order goods closer to the time you need them.
The OLTQuote formula determines the time between the customer's quote date and the order entry date. This is the difference between when the customer agrees to receive the material and when they place the order.
Here are the different OLT formulas:
- OLTRequested = Wish Date – Order Entry Date
- OLTQuote = Quote Date – Order Entry Date
- OLTActual = Delivery Date – Order Entry Date
- OLTConfirmed = Confirmed Date – Order Entry Date
Understanding the OLTConfirmed formula is essential for businesses to know when they can expect delivery. This formula calculates the time between the confirmed delivery date and the order entry date.
By using OLT formulas, businesses can make informed decisions about their inventory management and reduce costs.
How to Calculate
To calculate the time between order and delivery, you need to break it down into individual components. The delivery lead time is the time it takes for a customer's order to be processed, shipped, and finally received.
Start by identifying the key components that contribute to the delivery lead time, such as Order Processing Time, Processing and Preparation Time, Transit Time, Shipping and Handling Time, and Delivery Time.
Here are the specific formulas to calculate each component:
- Order Processing Time = Time of order approval – Time of order placement
- Processing and Preparation Time = Time of product readiness – Time of order approval
- Transit Time = Time of delivery – Time of shipment departure
- Shipping and Handling Time = Time of shipment handover – Time of shipment departure
- Delivery Time = Time of delivery – Time of shipment arrival at local distribution center
You can also calculate the OLT (Order-to-Delivery Time) by determining the difference between the date the customer wants the material and the date when they provided the order to the supplier, or between the date the customer agreed to receive the material and the date when the order was provided to the supplier.
To calculate the total delivery lead time, simply add up the times calculated for each component.
Here's a summary of the components and their formulas:
By breaking down the delivery lead time into individual components, you can identify areas for improvement and optimize your order fulfillment process.
Supply Chain Management
Lead time in a supply chain management context refers to the time from when a customer places an order to when it's ready for delivery. This can be broken down into internal lead time, which is the time required for a buying organization's internal processes to progress from identifying a need to issuing a purchase order, and external lead time, which includes the time required for the supplying organization's processes, including development, manufacture, dispatch, and delivery.
Related reading: When Transporting a Delivery Order That Contains Alcohol
Total lead time is a combination of internal and external lead time. Reducing both material flow lead time and information lead time is necessary to secure supply chain performance improvements. Information enriched supply chains are crucial in this context.
To minimize lead times for raw materials or products, it's essential to collaborate closely with suppliers and encourage efficient production and prompt delivery of supplies. This can support quicker fulfillment and better customer experience.
Supply chain disruptions, such as lack of raw materials, labor shortages, and natural disasters, can offset order lead times. To counteract these challenges, it's best to give vendors ample time to fulfill orders and maintain a healthy level of safety stock at the warehouse.
Supply chain inefficiencies can be caused by bottlenecks with shipping methods, creating long lead times. Improving shipping strategies, such as using flat rate or priority shipping, and placing more timely purchase orders can increase supply chain efficiency.
Lead time is crucial for order management, as it helps businesses plan and schedule their purchase orders. By knowing how long it takes to receive goods, sellers can create purchase orders to ensure they have enough inventory to meet customer demand.
Here's an interesting read: Order Fulfillment in Supply Chain Management
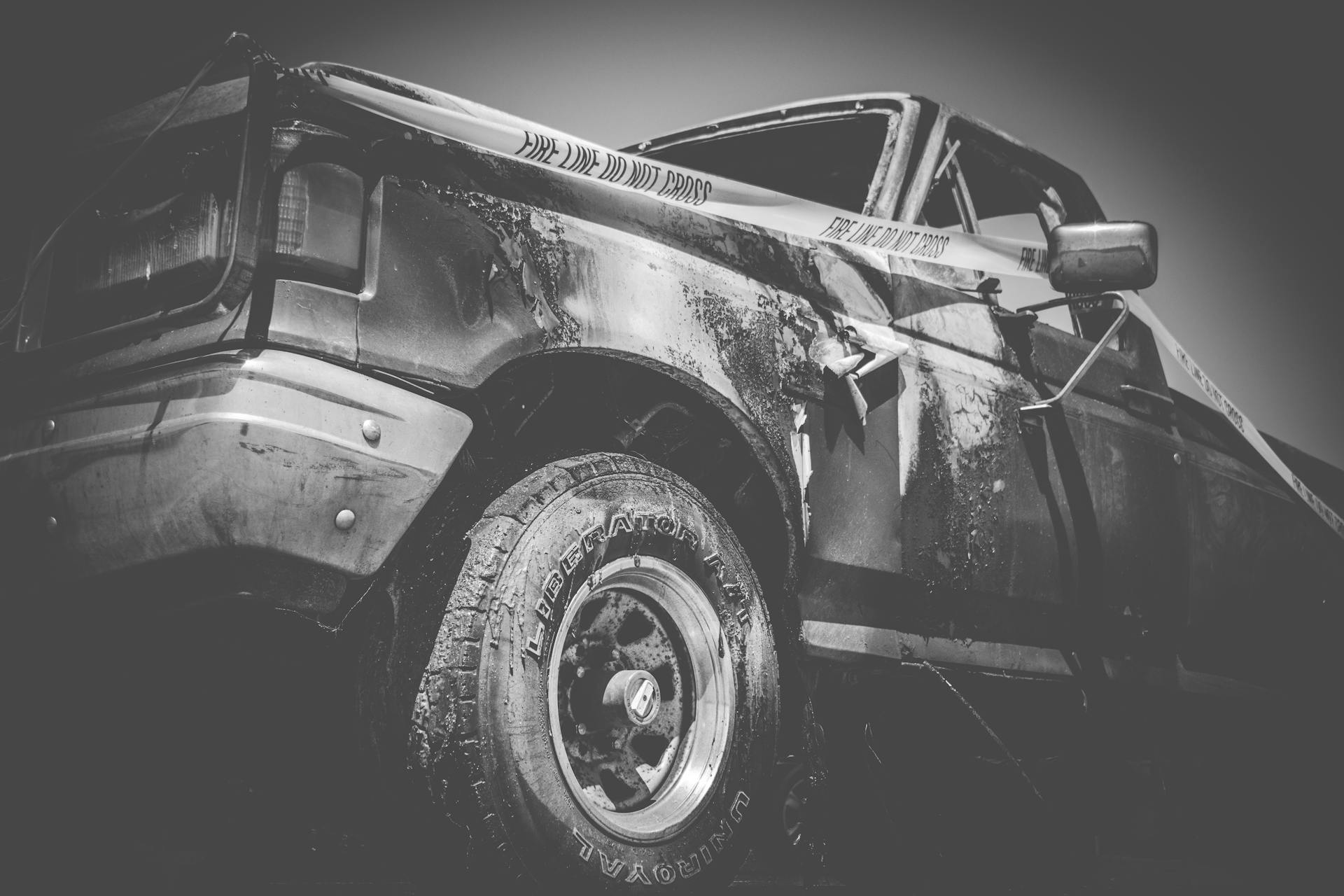
A well-organized warehouse layout can help optimize the flow of goods and reduce the steps taken to fill orders. This can include reducing walking distances, minimizing redundant tasks, and streamlining the process from receiving raw materials to finished shipping products.
Efficient delivery lead times reflect streamlined processes, optimized logistics, and synchronized coordination. A shorter lead time often translates to lower inventory carrying costs, as products spend less time in storage.
Reducing OLT
Reducing OLT is crucial to improving customer satisfaction and reducing lead times. By analyzing the difference between the customer's desired delivery date and the actual delivery date, you can identify areas for improvement.
One way to reduce OLT is to provide customers with accurate lead times. This can be done by calculating the OLTRequested, which is the difference between the customer's wish date and the order entry date. For example, if a customer wants to receive a shipment in 10 days and the order was entered 5 days ago, the OLTRequested is 5 days.
Explore further: Customer Order Fulfillment
To give customers a more realistic expectation, you can also calculate the OLTQuote, which is the difference between the quote date and the order entry date. This will help customers understand how long it will take to receive their shipment after they agree to the quote.
Here are the different types of OLT and their calculations:
By calculating and tracking these different types of OLT, you can identify areas where your delivery process can be improved and make changes to reduce lead times.
Expedited Shipping Options
Offering expedited shipping options is a simple yet effective way to reduce OLT. This allows customers to pay extra for faster delivery, catering to time-sensitive customers and generating additional revenue. By providing expedited shipping choices, businesses can attract new customers and influence purchase decisions.
Competitive differentiation is key in a crowded marketplace, and delivery lead time is a potent differentiator. Businesses that offer faster deliveries than competitors gain a unique advantage, positioning themselves as customer-centric organizations focused on convenience and reliability.
Guaranteeing quicker deliveries can even sway purchase decisions, especially if prices are slightly higher. This is because consumers value convenience and reliability, making expedited shipping options a valuable selling point.
How to Reduce
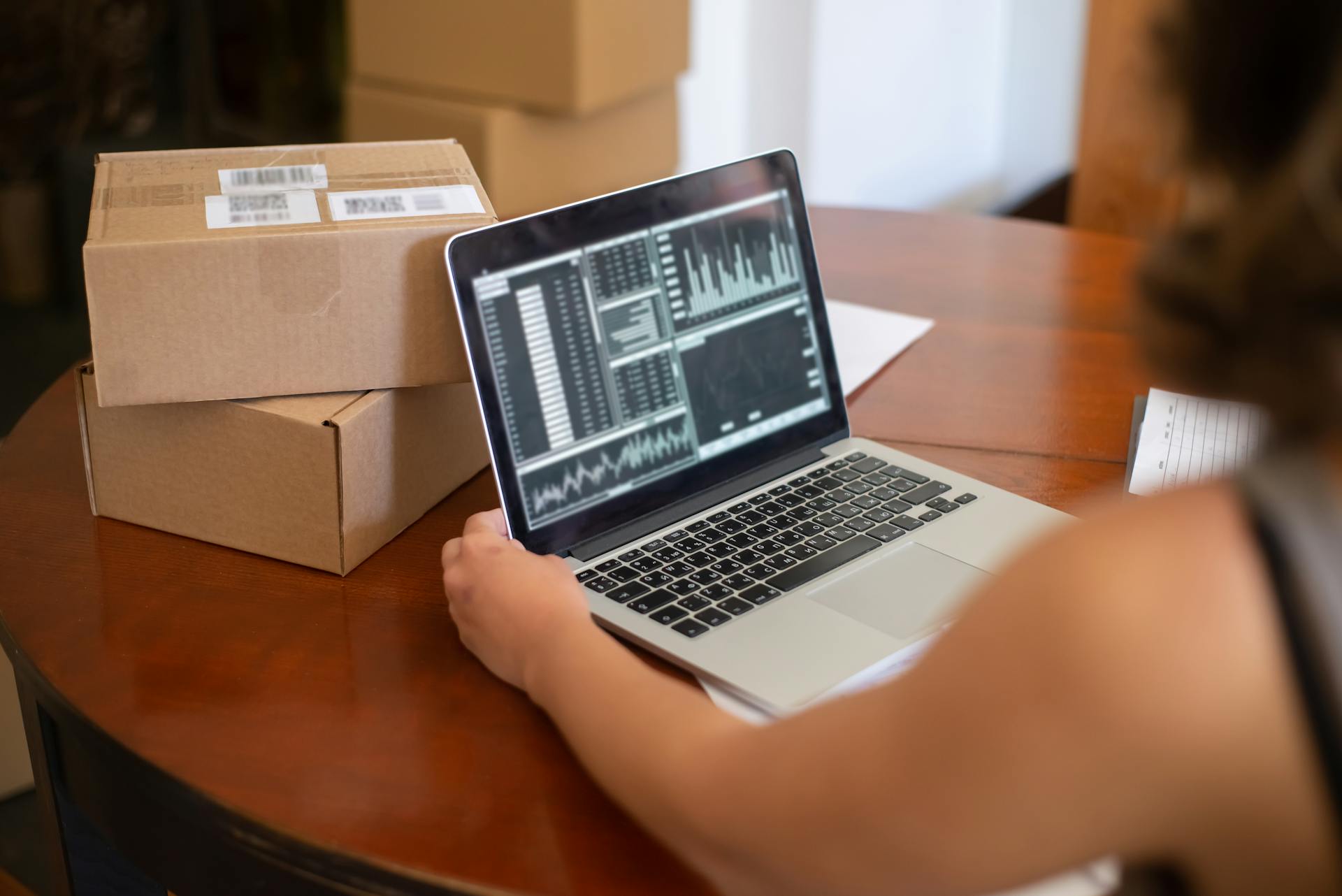
Reducing OLT requires a clear understanding of your inventory management. By optimizing lead time, businesses can reduce their inventory costs.
Knowing exactly how long it takes between reorders and delivery allows you to order goods closer to the time you need them. This reduces how much and how long you must hold stock in your warehouse.
To calculate the Average OLT based on Volume, you need to multiply the volume of product delivered by the OLT, then divide by the total quantity delivered in the period of time you're studying.
The formula for this calculation is: OLTV=∑ ∑ jQuantityj⋅ ⋅ OLTjTotalQuantityDeliver
Improving OLT
Improving OLT (Order Lead Time) is crucial for maintaining customer satisfaction and trust. A consistent and mutually agreed-upon time between purchase order placement and order delivery is essential for this.
To improve OLT, you can start by optimizing lead time, which can be done by analyzing any discrepancies or delays to identify areas for improvement. Regularly assess your delivery lead time calculations and processes to implement changes and optimizations to enhance overall efficiency.
To calculate OLT, you can use the following formulas:
- OLTRequested = Wish Date – Order Entry Date
- OLTQuote = Quote Date – Order Entry Date
- OLTActual = Delivery Date – Order Entry Date
- OLTConfirmed = Confirmed Date – Order Entry Date
By leveraging these formulas and regularly assessing your lead time data, you can identify areas for enhancement and implement changes to improve your OLT.
Implement Lean Practices
Implementing lean practices is a crucial step in improving Order Lead Time (OLT). It involves identifying and eliminating bottlenecks in the order fulfillment process.
To start, you need to identify non-value-added activities that waste time and resources. This can be done by analyzing your current processes and eliminating any unnecessary steps or tasks.
Lean practices can help you reduce wastage and allocate resources efficiently, accelerating the movement of orders through the supply chain. By streamlining your processes, you can reduce the time it takes to fill orders and improve overall efficiency.
Adopting lean principles can also help you identify areas for improvement and make targeted changes to optimize your supply chain. This can be achieved by leveraging data analytics to gain insights into historical performance and demand patterns.
By implementing lean practices, you can achieve significant improvements in your OLT and enhance your overall supply chain performance.
Collaborate with Logistics Partners
Collaborate with Logistics Partners is a crucial step in improving Overall Logistics Time (OLT). By forging strong partnerships with reliable logistics providers and carriers, you can optimize routes, schedules, and transportation methods.
This collaboration can lead to shipments moving swiftly from point to point. In fact, it's been shown that optimizing routes can reduce transportation time by up to 30%.
Worth a look: Tagg Logistics Order Fulfillment Center
OLT Tools and Software
OLT Tools and Software can help streamline the process of tracking time between order and delivery.
To determine the time between order and delivery, you'll need to use specific formulas. OLTRequested, OLTQuote, OLTActual, and OLTConfirmed formulas can be used to calculate the time between order entry and delivery.
These formulas are calculated by subtracting the Order Entry Date from the Wish Date, Quote Date, Delivery Date, and Confirmed Date, respectively.
Here's a quick rundown of the formulas:
- OLTRequested = Wish Date – Order Entry Date
- OLTQuote = Quote Date – Order Entry Date
- OLTActual = Delivery Date – Order Entry Date
- OLTConfirmed = Confirmed Date – Order Entry Date
Implementing inventory management software can also help streamline processes and reduce lead times. This type of software allows for real-time tracking of order status and accurate forecasting.
An enterprise resource planning (ERP) system can help reduce the time it takes to process and ship orders, resulting in shorter order cycle times.
Take a look at this: Software Order Fulfillment
Frequently Asked Questions
What is the period between order and delivery?
The period between order and delivery is known as delivery lead time. This metric measures the time it takes for an order to be fulfilled and delivered to the customer.
Featured Images: pexels.com