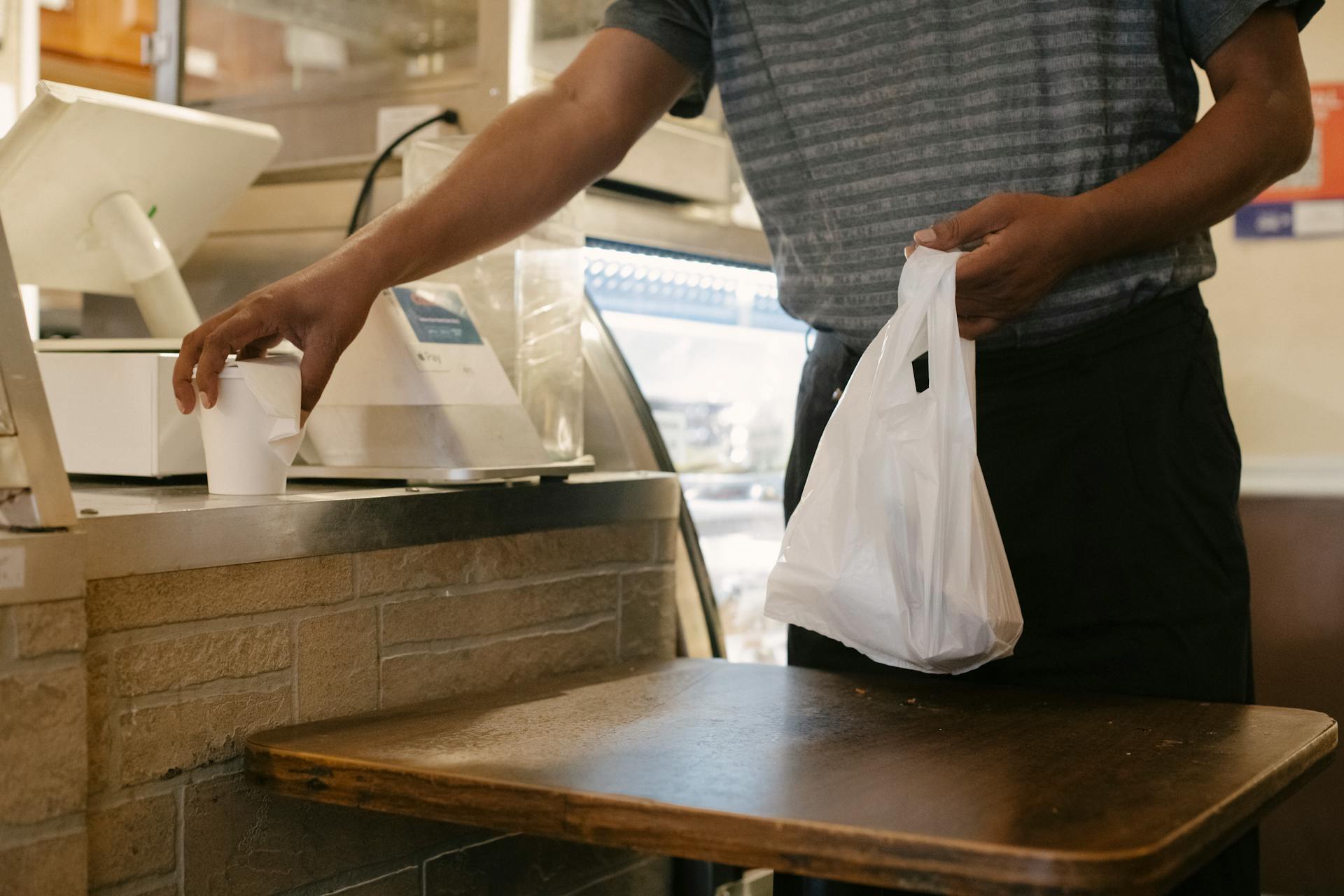
Order picking software is a game-changer for warehouse operations, allowing companies to streamline their processes and reduce errors.
Studies show that a well-implemented order picking system can reduce picking errors by up to 90% and increase productivity by 30%.
By automating tasks and providing real-time visibility into inventory and orders, order picking software can help warehouses operate more efficiently.
This can lead to significant cost savings, as companies can reduce labor costs, minimize inventory holding costs, and improve shipping times.
Benefits of Order Picking Software
Order picking software can have a significant impact on your business, and it's essential to consider the benefits it can bring. By implementing order picking software, you can improve inventory accuracy with real-time tracking of inventory levels.
Automating tasks and providing real-time data can help eliminate common picking errors. This can be seen in apps like OIS Inventory, which can boost productivity and streamline the order picking process. With the right software, you can reduce manual errors and ensure that every order is processed and fulfilled accurately and efficiently.
A Warehouse Management System (WMS) can also improve efficiency, reduce costs, and enhance customer satisfaction. Some of the key benefits of a WMS include improved inventory accuracy, optimized picking and packing, and streamlined shipping and receiving.
Using pick and pack software in your E-Commerce fulfillment process can make the picking and packing warehouse operations much easier for your warehouse workers. This can lead to faster and more accurate packing, with detailed packing slips generated to ensure everything gets shipped correctly.
Some of the benefits of order picking software include:
- Improved inventory accuracy
- Optimized picking and packing
- Streamlined shipping and receiving
- Enhanced labor management
- Data-driven insights
By implementing the right order picking software, you can increase picker productivity by 20-40% and eliminate paper pick tickets. This can be achieved through features such as batch picking, team picking, and zone picking functionality, which reduces walking and increases productivity.
Common Manual Mistakes and Errors
Manual errors in order picking can have serious consequences, including delayed shipments, incorrect product deliveries, and dissatisfied customers. In fact, 63% of respondents in a survey identified human error caused by managing manual processes as the primary reason for inventory or fulfillment problems.
Manual order picking is prone to errors that can cause delays, shipping inaccuracies, and customer dissatisfaction. Common manual errors include picking the wrong quantity, picking from the wrong location, and misreading the order or inventory count.
Here are some of the most common manual errors that occur during the warehouse order picking process:
- Picking the wrong quantity (Example 6)
- Picking from the wrong location (Example 7)
- Manual processes (Example 5)
- Inadequate training (Example 5)
- Poor warehouse layout (Example 5)
- Lack of technology (Example 5)
- Time pressure (Example 5)
These errors can lead to increased order returns and customer dissatisfaction, lost productivity due to rework, and increased labor costs due to the need to correct errors.
How Errors Impact Operations?
Manual errors in the warehouse order picking process can have severe consequences for warehouse operations. Increased order returns and customer dissatisfaction are just the beginning.
Lost productivity due to rework is another significant issue, as correcting manual errors requires additional time and resources. This can lead to inefficiencies in warehouse operations and impact the bottom line.
According to statistics, manual processes are a major contributor to warehouse picking errors. Relying on paper-based picking lists increases the risk of human error.
Inadequate training and poor warehouse layouts are also common culprits. Disorganized or inefficient warehouse layouts can lead to confusion and errors, making it difficult for warehouse staff to accurately locate and pick items.
The lack of technology is another factor that contributes to errors. Not using barcode scanners or other automation tools increases the likelihood of errors, making it essential to implement a reliable and accurate system for managing the entire order fulfillment process.
Here are some of the negative consequences of manual errors in warehouse operations:
By understanding the causes and consequences of manual errors, we can take steps to prevent them and improve warehouse operations.
Features and Capabilities of Order Picking Software
Order picking software is a game-changer for warehouses, and its features and capabilities are what set it apart from manual operations. Manual errors are a thing of the past with automated inventory tracking, which provides real-time visibility into inventory levels.
Barcode scanning integration is a must-have for efficient order picking, allowing pickers to quickly scan items and reduce errors. This feature is available in user-friendly native pick and pack apps that are easy to use, even for new employees.
Picking route optimization is a key benefit of order picking software, reducing the time and distance pickers need to cover inside the warehouse. This is achieved through software that considers all possible paths to reach warehousing positions and bins during the picking and packing process.
Batch picking, team picking, and zone picking functionality increases productivity by reducing walking, which can be a significant time-saver. On-screen prompting for the next pick also helps pickers stay on track and avoid errors.
Warehouse management systems (WMS) and order management systems (OMS) are software applications that help businesses manage and process customer orders. They automate order entry, track order status, and facilitate order fulfillment, making the process more efficient.
Real-time tracking is a critical feature of warehouse order picking software, allowing managers to monitor the status of orders and pickers in real-time. This feature ensures that all orders are being fulfilled on time and accurately.
Here are some key benefits of using order picking software:
- Improved inventory accuracy through real-time tracking
- Optimized picking and packing processes
- Streamlined shipping and receiving
- Enhanced labor management
- Data-driven insights for optimizing warehouse operations
These benefits can be achieved through the use of order picking software that offers features like automated inventory tracking, barcode scanning integration, picking route optimization, and real-time tracking.
Choosing the Right Order Picking Software
Choosing the Right Order Picking Software is crucial for efficient warehouse operations. It's essential to consider the compatibility and integration with existing systems, such as ERP integration and WMS systems.
To ensure seamless data flow, look for software that can integrate with popular solutions like QuickBooks Online and Desktop. This will eliminate manual data entry and simplify your warehouse operations and finances.
Some key benefits of order picking software include improved inventory accuracy, optimized picking and packing, and enhanced labor management. These benefits can be achieved through real-time tracking of inventory levels and efficient routing and task management.
Choosing the Right System
Choosing the right order picking software can be a daunting task, but let's break it down. You need a solution that can handle your unique business needs, whether you're a small or medium-sized business or a large enterprise.
To start, consider the level of automation you need. If you're looking to streamline your sales and supply chain management, a control and sales management solution like Lightning Pick's LP Pick can be a great choice. It's industry-leading and offers real-time statistics on picker productivity.
On the other hand, if you're looking for a more comprehensive warehouse management system, look for one that provides real-time visibility into inventory levels and optimizes picking and packing processes. A Warehouse Management System (WMS) like the one described in Example 2 can help you achieve this.
Another key consideration is the type of operations strategy you have. If you're looking to enable a partner to pick in-store or from a dark store, you'll want a system that allows for flexibility and scalability. Maximum Efficiency, described in Example 5, can help you set up your store to pick orders yourself or enable a partner to pick.
Here are some key features to look for in an order picking software:
- A flexible and reliable hardware platform
- Industry-leading order fulfillment execution software
- Real-time statistics on picker productivity and order volumes
- A quick training curve and start-up time
- Real-time visibility into inventory levels
- Optimization of picking and packing processes
Ultimately, the right system for you will depend on your specific business needs and operations strategy. Take the time to research and compare different options, and don't be afraid to ask for demos or trials before making a decision.
Total Cost of Ownership (TCO)
Total Cost of Ownership (TCO) is a crucial factor to consider when selecting order picking software. The upfront cost of the software is just the beginning, as ongoing maintenance and support costs can add up quickly.
The software should provide a good return on investment (ROI) by improving efficiency and reducing errors in the order picking process. This can lead to significant cost savings and a higher overall value.
Grocery Retailers
If you're a grocery retailer looking to boost your online order picking speed and efficiency, you're in luck. StrongPoint's solution can help you achieve world-leading picking rates.
Grocery retailers need to deliver accurate orders to their customers, and StrongPoint's solution can help with that.
To improve delivery accuracy, consider a solution that prioritizes customer service. This is exactly what StrongPoint's solution does, delivering a seamless experience that customers will love.
By using StrongPoint's solution, grocery retailers can also reduce errors and increase customer satisfaction.
Zebra Technologies Compatible Application
ProCat's partnership with Zebra Technologies has been a long-standing one, spanning over 10 years. This collaboration has enabled our software solutions to run seamlessly on Zebra-manufactured devices.
ProCat's software solutions have been designed to integrate with Zebra Technologies devices, making it a reliable choice for businesses.
PickRight, our order picking software, has been designated as a Zebra Technologies Compatible application, which is a testament to our company's commitment to quality and compatibility.
Testimonials
Many businesses have seen significant improvements in accuracy with order picking software, with one company reporting far more accuracy than when they were using paper.
We've seen firsthand how tedious it can be to dig through piles of paper to research orders, and it's a huge time-saver to have reports that make the process easier.
Businesses like the one that saved hours of time not having to dig through piles of paper to do research can attest to the efficiency of order picking software.
Implementation and Integration
Implementation and Integration is a crucial step in getting the most out of your order picking software. Compatibility with existing systems is essential to avoid manual data entry and errors.
ERP integration is a must-have to ensure seamless data flow between systems. Inventory management apps like OIS Inventory excel in this area, integrating with popular solutions like QuickBooks Online and Desktop.
This integration will simplify your warehouse operations and finances by eliminating manual data entry.
Integrate with Automation
Integrating with automation is a key part of any successful implementation. StrongPoint’s solution is fully integrated with automated systems to handle fast-movers, ensuring maximum efficiency.
This level of integration allows for seamless communication between different systems, reducing the need for manual intervention and minimizing errors.
Automated systems can also help to streamline processes and reduce labor costs, freeing up staff to focus on higher-value tasks.
StrongPoint’s solution is designed to work in harmony with existing automated systems, ensuring a smooth and efficient workflow.
Compatibility and Integration
Compatibility and integration are crucial for a smooth warehouse operation.
ERP integration is a must-have for seamless data flow between systems.
Inventory management apps like OIS Inventory excel in this area, integrating seamlessly with popular solutions like QuickBooks Online and Desktop.
Manual data entry is a thing of the past with integrated systems.
ProCat's PickRight software is a Zebra Technologies Compatible application, running on devices manufactured by Zebra.
This partnership has been ongoing for over 10 years, demonstrating the importance of compatibility and integration.
A compatible application like PickRight ensures that data flows freely between systems, reducing errors and improving efficiency.
By choosing a compatible and integrated system, you can simplify your warehouse operations and finances.
Instantly Scalable
One of the key benefits of order picking software is its ability to scale quickly and efficiently. StrongPoint's solution can onboard stores in under a day.
This means you can start using the software right away, without having to wait for a lengthy implementation process. Combine it with Electronic Shelf Labels for an even faster experience.
With StrongPoint's solution, pickers can be trained in just 10 minutes, making it easy to get started with the software.
Frequently Asked Questions
What are the three main picking systems?
The three main picking systems used in warehouses are batch picking, zone picking, and wave picking. These systems can be used separately or in combination to meet specific warehouse needs.
Sources
- https://ordersinseconds.com/reduce-errors-with-warehouse-picking-software/
- https://www.pulpowms.com/warehouse-picking-and-packing-software
- https://www.skusavvy.com/blog/the-best-pick-pack-software
- https://www.strongpoint.com/solutions/e-commerce-order-fulfillment/order-picking/
- https://www.procatdt.com/solutions/pickright/
Featured Images: pexels.com