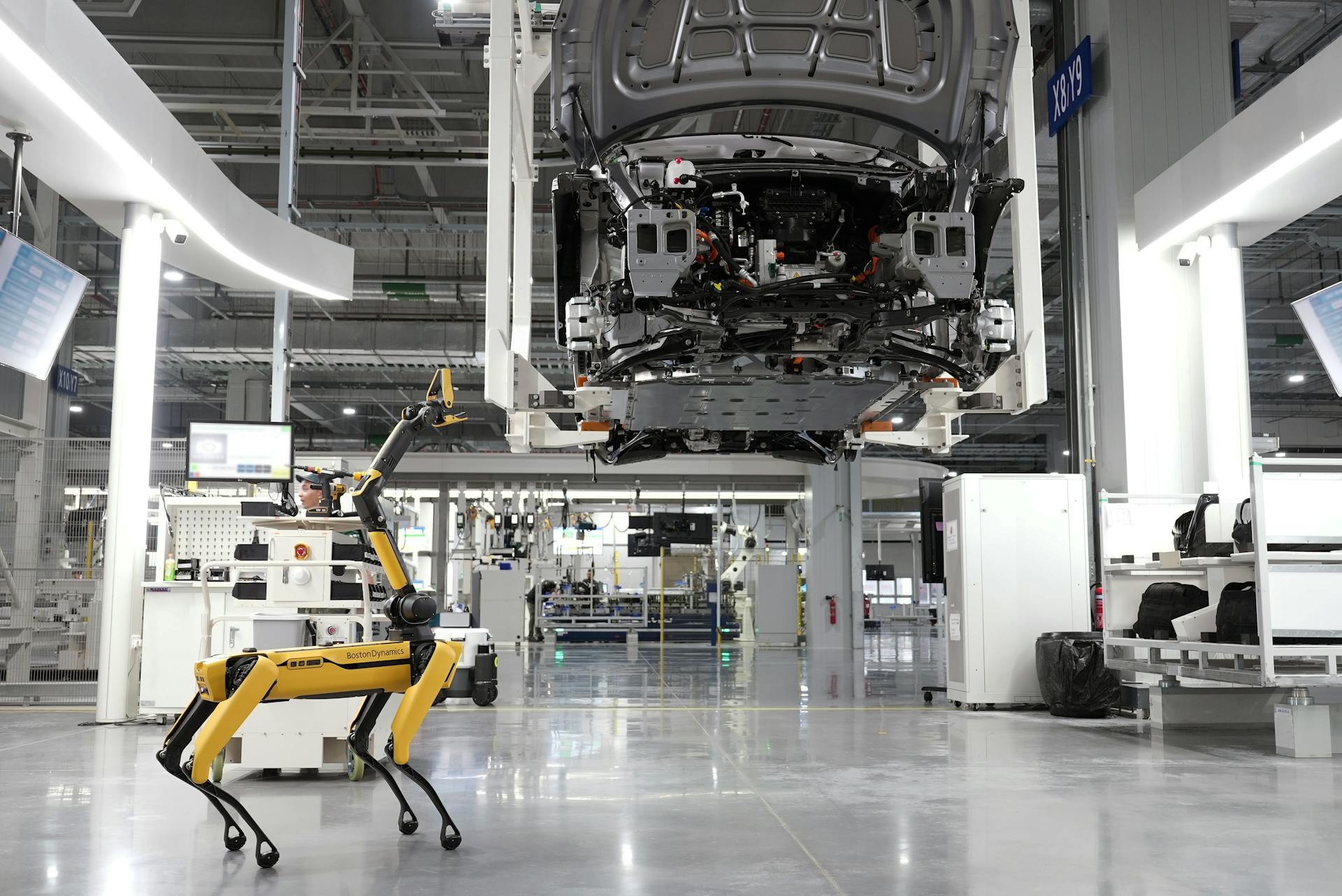
Order picking systems and strategies can make a huge difference in productivity. According to research, a well-designed order picking system can increase efficiency by up to 30%.
To achieve this, companies often implement zone picking, which involves dividing the warehouse into separate zones based on product categories. This helps reduce travel time and increase picking accuracy.
A study found that zone picking can reduce travel distances by up to 50%. By minimizing travel time, workers can focus on picking and packing orders more efficiently.
Companies also use voice-directed picking, which guides workers through their tasks using voice commands. This technology can reduce errors by up to 25% and increase picking speeds by up to 15%.
What is Order Picking?
Order picking is the process of selecting items from a warehouse's stock to fulfill customer orders. It's a crucial step in delivering client orders and requires speed and precision.
Efficiency is key to the order-picking process, as the time it takes to prepare an order significantly impacts the timeliness of its shipment. Customer satisfaction may be impacted by how quickly and accurately orders are picked and packed for shipment.
Order picking involves picking the right product, in the correct quantity, at the right time for dispatch. It's a complex process that requires careful planning and execution, involving several steps such as receiving customer orders and preparing them for shipment.
What Is?
Order picking is the process of selecting items from a warehouse's stock to fulfill customer orders. It's hard work that requires speed and precision.
Efficiency is crucial to the order-picking process since the time it takes to prepare an order significantly impacts the timeliness of its shipment. This can affect customer satisfaction and ultimately, the success of a business.
Order pickers spend most of their time searching through a specific warehouse for the products to fulfill customer orders. This is why forward-thinking businesses can implement methods to reduce the distance and time required for order pickers to find the products they need.
Order picking allows warehouse operators to efficiently fulfill customer orders by choosing the correct SKUs from inventory. This is thanks to picking systems such as picker robots and voice-picking systems.
The order-picking process involves several steps, including receiving customer orders, locating and picking appropriate items, and preparing them for shipment. It's a complex process that requires careful planning and execution.
Order picking makes up as much as 55% of the operating expenses of a warehouse. This is why optimizing order-picking efficiencies is so important to maintaining the highest level of customer satisfaction.
Discrete
Discrete order picking is a common strategy used in warehouses due to its simplicity and straightforward implementation.
Individual goods are selected by pickers until the order is complete, making it a great option for warehouses with fewer orders and stock fewer SKUs.
This approach works well for warehouses that get fewer orders and stock fewer SKUs.
The turnaround time for fulfilling orders is much reduced with discrete picking.
It's simple to monitor the precision of the order pickers, which is a big advantage of this method.
However, discrete picking is a labor-intensive and inefficient method for warehouses that deal with higher-volume or more complicated orders due to the time spent traveling between picking locations.
Types of Order Picking Methods
There are various order-picking methods used in warehouses today. The picker-to-component system is a popular strategy that streamlines the order-selecting process by using forklifts to move goods throughout the material handling section.
In this system, order pickers use the picking area to assemble orders for shipments. They search the warehouse to locate specific products requested by customers.
Some common picking methods include picker-to-part, batch picking, and wave picking. These methods provide a flexible workflow, but also require more time spent traveling.
Here are some key characteristics of each method:
Types of Methods
There are many types of order-picking methods used in warehouses today.
Some organizations use a single method, while others combine multiple methods to optimize their picking processes.
To optimize picking processes and the entire order fulfillment process, it’s essential to find the picking methods and strategies that work best for your organization.
Common picking methods in the warehouse include batch picking, where multiple orders are picked together, and zone picking, where orders are picked from specific zones within the warehouse.
Picking methods can be optimized to suit the size and layout of the warehouse, as well as the type and volume of orders being fulfilled.
Combined Methods
If none of the individual order-picking methods seem right for you, you can try combining two of the aforementioned methods. This is a great way to tailor your picking process to your specific warehouse needs.
Combining order-picking methods can be beneficial for warehouses with a high volume of orders, as it allows for more efficient use of labor and warehouse resources. By combining methods, you can optimize your picking process and reduce congestion in the warehouse.
One popular combination is batch-and-sort zone-picking, where workers in each zone pick items for multiple orders. This method helps reduce congestion and increases order-picking speed.
Another combination is wave picking with zone-picking, where orders are grouped into sets or waves based on factors like customer location or order frequency. Workers then pick SKUs from multiple zones and forward them for sorting and consolidation into individual shipments.
Here are some benefits of combining order-picking methods:
- Reduces congestion in the warehouse
- Increases order-picking speed
- Optimizes labor and warehouse resources
By combining order-picking methods, you can create a picking process that is tailored to your specific warehouse needs and helps you achieve your goals.
Manual Order Picking Methods
Manual order picking methods can be a bit old-school, but they still have their place in the right situations. Let's take a look at some of the most common methods.
Pick and Pack, also known as Discrete Picking or Single-Order Picking, is a method that involves picking and packing individual orders one at a time. It works well for businesses with a small number of orders, like a retail fulfillment warehouse servicing 40 stores a day.
One of the main advantages of Pick and Pack is its ease of implementation. This is because it doesn't require a lot of complex systems or technology to set up. Plus, order picker accuracy and performance are easily tracked.
However, Pick and Pack also has some downsides. It can be quite time-consuming and labor-intensive, which can lead to excessive picker travel. This can be a major issue in warehouses with a high volume of orders.
Automated Order Picking Methods
Automated Order Picking Methods can greatly improve efficiency in warehouses.
Automated warehouse picking can be integrated with your current warehouse management system to facilitate precise picking and packaging. This can benefit your company regardless of the industry.
Pick-to-light, voice-directed picking, and vision picking systems have been shown to reduce manual labor, boost productivity, and improve accuracy in various warehousing operations.
Robotics, such as goods-to-person technologies and autonomous mobile robots, are becoming increasingly common in warehouses. They can work around the clock, reducing errors and increasing productivity.
A dedicated picking software can be used to increase accuracy and customer satisfaction by providing real-time visibility and better inventory control.
Benefits and Best Practices
Using an order picking system can greatly benefit your business by streamlining the picking process, allowing you to quickly fulfill customer orders without sacrificing quality.
A streamlined picking process gives you the best opportunity to quickly fulfill customer orders without sacrificing quality. This is especially true when you implement the right picking method and system, such as zone picking, which can help make better use of warehouse space.
Warehouse space is a valuable resource, and using it efficiently can make a big difference in your operations. Certain picking methods, such as zone picking, can help make better use of warehouse space.
Investing in the right picking systems is just the first step – implementing best practices is also crucial. Warehouse order picking best practices you should implement include using a Warehouse Management System (WMS) to optimize picking routes and reduce mispicks.
A WMS can analyze the order and determine the most efficient route based on the items’ locations. For example, if a customer orders a pair of shoes, a jacket and backpack, the WMS can direct the picker to start at the footwear section, move to outerwear and finish at the accessories area, if this is the shortest possible path.
Implementing a WMS can also improve overall productivity and create a unified and efficient warehouse management experience. Modula’s warehouse management system is designed to seamlessly integrate with their advanced automated storage and retrieval systems, creating a unified and efficient warehouse management experience and improving overall productivity.
Technology and Equipment
Technology and equipment play a vital role in improving order picking efficiency and accuracy. Heavy-duty picking equipment, such as forklifts, reach trucks, and order pickers, can boost warehouse operations by enhancing efficiency, picking accuracy, safety, and productivity.
Using the right equipment can also improve safety and achieve efficiency in the picking process. This includes using automated storage and retrieval systems to reduce physical strain and utilizing AMRs for picking efficiency.
Mobile scanning software and collaborative mobile robots can also help streamline order picking activities. Mobile scanning software can instantly confirm orders and monitor and allocate pick tasks, eliminating manual picking mistakes and increasing worker output. Collaborative mobile robots can assist in order picking activities by handling the manual task of moving products around, minimizing walking through real-time route optimization.
Here are some examples of technology and equipment that can be used in order picking:
- Forklifts: Lifts and transports heavy loads, especially palletized products
- Reach trucks: Retrieves items from high shelves in narrow aisles
- Order pickers: Lifts warehouse pickers to the level of high racks for picking individual goods
- Mobile scanning software: Instantly confirms orders and monitors and allocates pick tasks
- Collaborative mobile robots: Assists in order picking activities by handling the manual task of moving products around
Voice
Voice technology is revolutionizing the way warehouses operate, freeing up workers to focus on their tasks.
Voice-picking solutions are digital, hands-free technologies that guide warehouse workers to specified places inside a warehouse and inform them which SKU to choose to complete client orders with simple, easy-to-understand voice prompts.
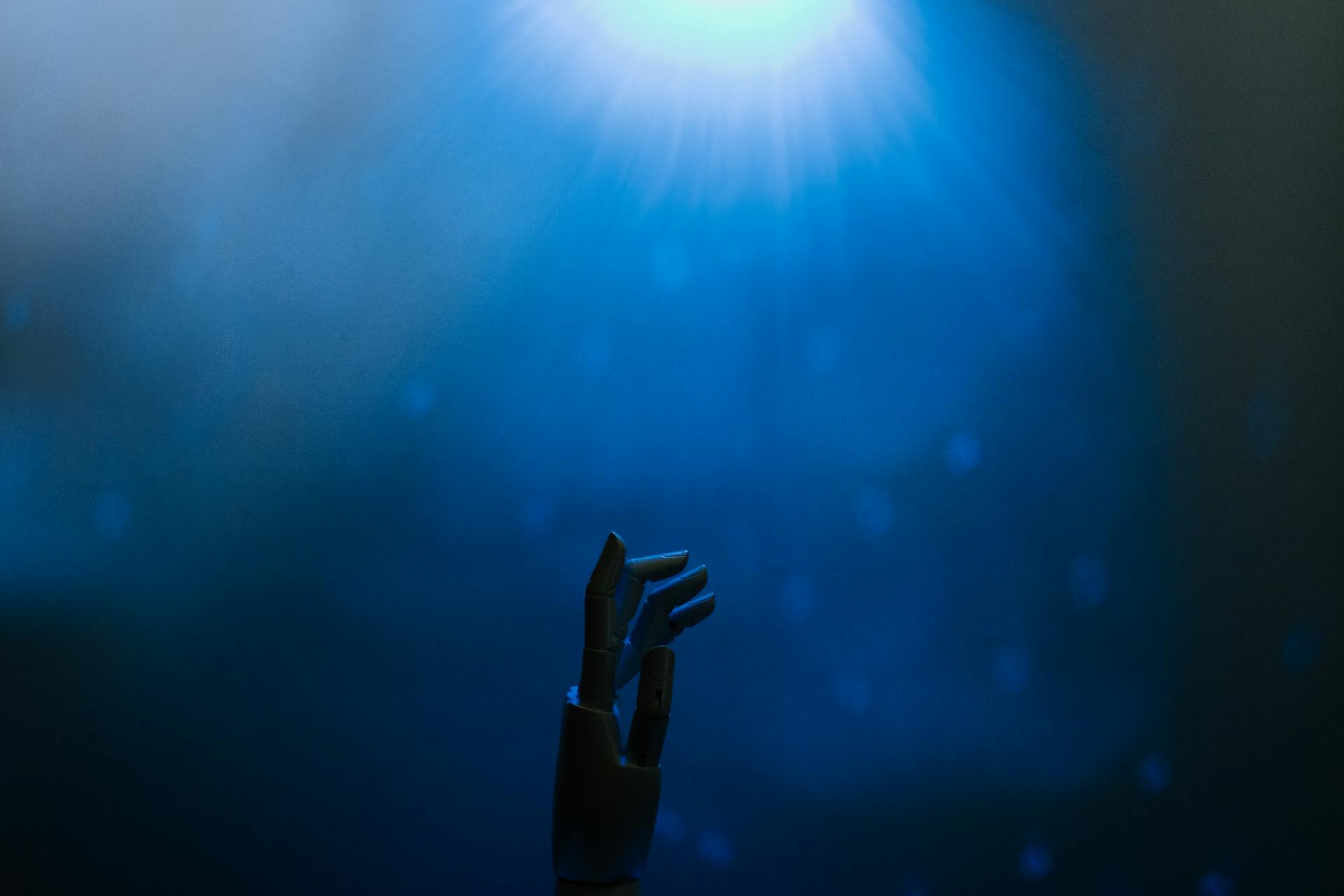
These systems are increasingly common in warehouses, helping pickers concentrate on their work by freeing their hands and eyes from other tasks.
With voice picking, pickers receive verbal instructions on what items to pick and the items' locations in real-time, sent through headsets connected to an order management system.
Warehouse employees receive verbal commands on which items to pick and where to find them, allowing them to keep their hands and eyes free for the task.
Voice-picking systems utilize voice prompts and advanced speech recognition software to communicate picking instructions to warehouse employees through headsets, speeding up the picking process and improving accuracy.
Pickings are verbally confirmed as complete, streamlining the process and reducing errors.
Mobile Scanner
Mobile scanners have revolutionized the picking process by instantly confirming orders and monitoring pick tasks, eliminating manual mistakes and increasing worker output.
Mobile scanning software is ideal for businesses looking to improve order accuracy and customer satisfaction. It's a game-changer for warehouses that want to streamline their operations and reduce errors.
With mobile scanner-based picking, workers are equipped with scanners that display pick lists and the location of each SKU. This helps them pick items more efficiently and accurately.
If a worker scans an item not on the pick list, the mobile scanner notifies them of the error. This error-detection feature is a huge plus for warehouses that want to improve picking accuracy.
Barcodes and scanners have greatly improved order-picking accuracy and speed, reducing errors and streamlining warehouse management.
Heavy-Duty Equipment
Heavy-duty equipment is a game-changer for warehouse operations. It boosts efficiency, picking accuracy, safety, and productivity.
Forklifts are a type of heavy-duty equipment that lift and transport heavy loads, especially palletized products. Reach trucks, on the other hand, are designed to retrieve items from high shelves in narrow aisles.
Order pickers are another essential piece of equipment that lifts warehouse pickers to the level of high racks for picking individual goods. This saves time and reduces the risk of injury.
Some common types of heavy-duty equipment include:
- Forklifts
- Reach trucks
- Order pickers
- Stackers
These machines are not only efficient but also help reduce manual labor, which can lead to fatigue and errors. By using heavy-duty equipment, warehouses can increase productivity and accuracy, ultimately leading to better customer satisfaction.
Role of Robotics and Software
Robotics and software are becoming increasingly common in warehouses, working around the clock to reduce errors and increase productivity.
Collaborative mobile robots, for example, can assist in order picking activities by handling the manual task of moving products around, minimizing walking through real-time route optimization.
These robots can be programmed to follow discrete, batch, zone, and cluster picking methods, and leverage artificial intelligence and machine learning to optimize picking routes and tasks in real-time.
Collaborative robots, or cobots, are advanced warehouse robotics designed to work alongside warehouse employees to enhance efficiency and productivity.
They are equipped with sensors and built-in safety features for seamless collaboration, and can be used for tasks like palletizing and picking and packing orders.
A dedicated picking software can be used to increase accuracy and customer satisfaction, and can be utilized to achieve synchrony between robotic systems and have better inventory control, labor management, and real-time visibility.
Robotics, such as goods-to-person technologies and autonomous mobile robots, can decrease the physical workload on human workers, leading to a safer work environment.
In conclusion, effective and efficient order picking is critical to warehouse operations, and investing in the right technology and equipment can yield significant benefits.
Layout
The layout of your warehouse is crucial for efficient operations. Arranging your warehouse to streamline the flow of goods can significantly reduce travel time for pickers.
By placing the most frequently picked items near the shipping area, you can minimize the distance pickers need to travel. This speeds up the entire picking process.
Warehouse size also plays a significant role in the order-picking process. Larger warehouses may benefit from zone or wave picking to make optimal use of resources.
The layout must be carefully considered, as the arrangement of products can affect picking efficiency.
Dashboard and Analytics
StrongPoint's software runs on a cloud-based solution, making it easily accessible from anywhere. This cloud-based setup allows for seamless tracking and management of your operations.
The back-office is accessed through a web interface, providing a convenient and user-friendly way to monitor your operations. You can access the back-office from any device with an internet connection.
In the back-office, you can see the picking speed of each individual employee, which is a valuable metric for evaluating their performance. This data can help you identify areas for improvement and optimize your workflow.
You can also configure the picking routes, which is a crucial aspect of optimizing your operations. By fine-tuning your picking routes, you can reduce errors and increase efficiency.
Additionally, you can configure the picking zones, allowing you to tailor your operations to your specific needs. This level of customization is a key benefit of StrongPoint's software.
Implement a Management System
Implementing a warehouse management system can greatly improve your order picking efficiency.
A well-designed WMS can analyze orders and determine the most efficient picking route based on the items' locations.
This is especially helpful for orders with multiple items, like a pair of shoes, a jacket, and a backpack.
The system can direct the picker to visit the items in the shortest possible path, like starting at the footwear section, moving to outerwear, and finishing at the accessories area.
Modula's warehouse management system is a top-notch solution that integrates seamlessly with automated storage and retrieval systems.
It's also very intuitive and can interface with nearly all DMS and ERP systems, making it easy to optimize processes like receiving, storing, and picking.
Efficiency and Scalability
Achieving efficiency and scalability in order picking is crucial for warehouses. Having an effective picking method enables a warehouse to adapt more easily to changing order volumes and business expansion.
Peak periods like holidays or sales seasons require scalability to maintain service quality. An efficient facility maximizes productivity while minimizing expenses, which is essential for handling high volumes of orders.
With the right solutions, stores can be onboarded in under a day, and pickers can be trained in just 10 minutes. This instant scalability helps warehouses respond quickly to changes in order volume.
-Batch-Wave
Batch-Wave Picking is a highly efficient approach that combines the benefits of batch and wave picking methods. It allows pickers to select all products for orders from their designated zone simultaneously.
This method is particularly useful for warehouses with high order volumes, as it can handle large numbers of orders with greater efficiency. By leveraging batch and wave picking techniques, warehouses can streamline their order-picking process and reduce errors.
In fact, studies have shown that with StrongPoint's solution, stores can be onboarded in under a day, and pickers can be trained in just 10 minutes, making it an instantly scalable solution.
Boost Efficiency
Boosting efficiency in your warehouse is crucial for maximizing productivity and minimizing expenses. A streamlined warehouse picking system can improve efficiency and accuracy for your warehouse staff. Picking efficiency and accuracy may be increased by providing workers with optimal routes that include validations and images to verify they are retrieving the correct items from the order.
Some warehouses have achieved impressive picking speeds, with customers averaging 240 items per hour, and some reaching up to 350. This highlights the importance of having a efficient order picking process in place.
Optimizing the order-picking process can help gain an efficient system, increasing productivity while reducing order error. This not only reduces facility expenses but also improves customer satisfaction, a key to maintaining and growing future business.
Warehouses with high order volumes might lean toward methods like batch or wave picking, which can handle large numbers of orders simultaneously with greater efficiency.
Industry and Integration
In the world of order picking, integration is key to maximizing efficiency. StrongPoint's solution is fully integrated with automated systems to handle fast-movers.
This seamless integration enables order pickers to focus on picking orders efficiently, rather than worrying about manual processing. StrongPoint's solution ensures that orders are processed quickly and accurately.
By integrating with automation, order picking operations can run smoother and more efficiently, resulting in increased productivity and reduced errors.
Cloud
Cloud-based solutions have made it easier for warehouses to implement zone picking strategies. Zone picking involves dividing the facility into several zones and assigning pickers to specific areas.
Each picker is responsible for gathering goods within their designated zone and passing the order to the next zone until all items in the order are picked. This approach has been shown to increase efficiency and reduce errors.
There are two common types of zone picking, but the core idea remains the same: to divide the warehouse into manageable areas and assign pickers to each zone.
Outsourcing 3PL Fulfillment
Outsourcing 3PL fulfillment can be a game-changer for businesses that lack resources or space.
Partnering with a 3PL can help you expertly handle warehousing and fulfillment needs, especially if you're scaling operations.
A 3PL can implement advanced technologies and proven strategies to reduce the time and cost associated with fulfilling orders.
Automated picking systems and optimized warehouse layouts can significantly reduce the time and cost associated with fulfilling orders.
At Modula, they help you streamline the picking process with automation, reducing mispicks and increasing speed and accuracy.
Their solutions, such as Put to Light systems and automated storage and retrieval systems, are designed to improve efficiency throughout your warehouse operations.
Product Nature
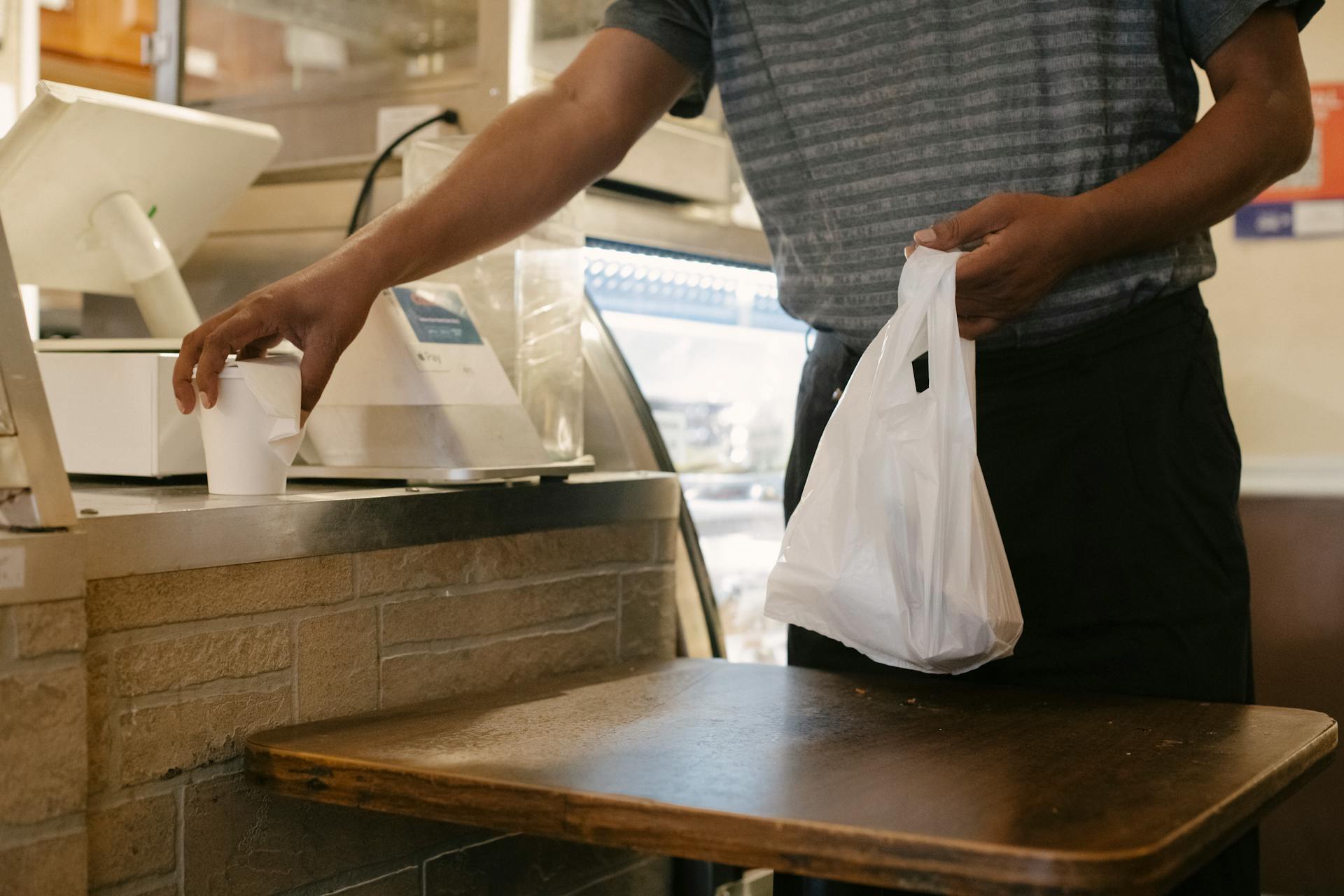
Product Nature plays a crucial role in determining the picking method. The type of products stored influences the picking method, with perishable items or those requiring special handling involving specific picking procedures.
Perishable items, such as food or pharmaceuticals, need to be handled with care to maintain their quality. This often requires specialized equipment and procedures to prevent spoilage or contamination.
Items that require special handling, like fragile or heavy products, may need to be picked and placed with extra caution. This can involve using specialized packaging or handling equipment to prevent damage.
Delivery Platforms
Delivery Platforms are a key player in the e-commerce industry, and StrongPoint's solution can help them improve their order picking process.
For Q-commerce delivery platforms that offer grocery delivery, StrongPoint offers a fully integrated picking module that complements their existing app. This module adds value to their service and helps them deliver a seamless experience to their customers.
Delivery platforms can achieve world-leading picking rates with StrongPoint's solution, which is a game-changer for their business.
StrongPoint's solution is designed to improve the speed, accuracy, and efficiency of order picking, making it an essential tool for delivery platforms.
Frequently Asked Questions
Is order picking hard?
Order picking is a physically and mentally demanding job, but with great career prospects for those who are organized and efficient. It requires strong organizational skills to arrange and pick products accurately.
What does it mean when an order is in picking?
When an order is in picking, it means our warehouse team is selecting the items from our stock to fulfill your order. This is the first step in getting your order ready for shipping
Sources
Featured Images: pexels.com