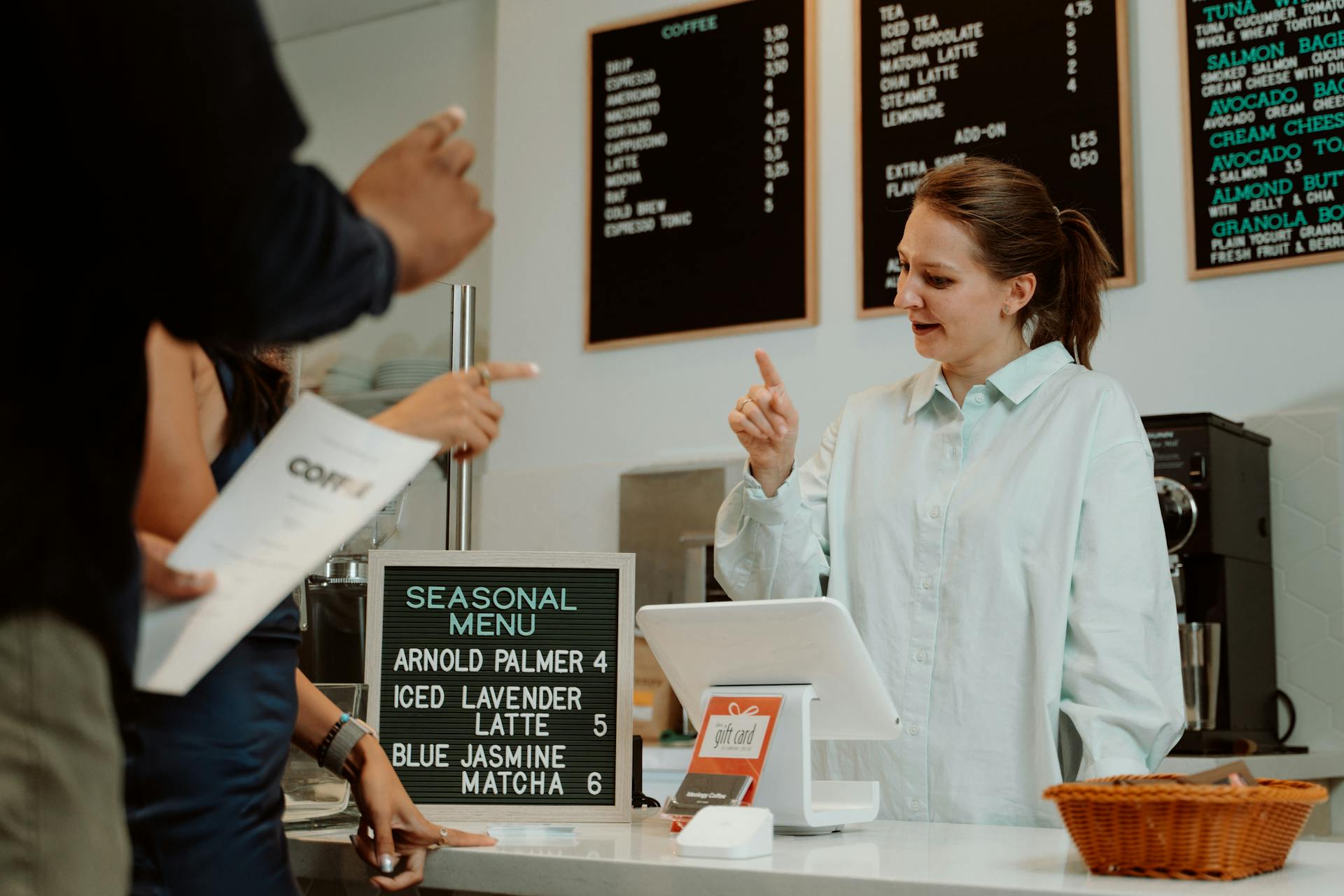
A high order fulfillment rate is crucial for businesses to maintain customer satisfaction and loyalty. According to research, a 1% increase in order fulfillment rate can lead to a 5% increase in customer retention.
Order fulfillment rate is the percentage of orders that are fulfilled correctly and on time. It's a key performance indicator (KPI) that measures the efficiency of a supply chain. A good order fulfillment rate is typically above 90%.
A low order fulfillment rate can lead to increased costs, damaged reputation, and lost customers. It's essential to identify the root cause of the issue and implement corrective actions to improve the rate.
What is Order Fulfillment Rate?
The order fulfillment rate measures the percentage of customer orders dispatched from available stock. This metric reflects a company's efficiency in the order filling process and mirrors their ability to meet customer demand.
A high order fulfillment rate indicates effective inventory management and robust supply chain strategies. These are crucial for operational success and maintaining a high warehouse fill rate.
Monitoring order fulfillment metrics helps businesses identify areas for improvement within their supply chain. This can lead to a reduction in customer complaints and enhanced overall satisfaction.
Maintaining a high order fulfillment rate minimizes customer complaints and enhances overall satisfaction. It's a key indicator of a company's ability to meet customer demand and optimize operational performance.
Calculating Order Fulfillment Rate
Calculating order fulfillment rate is a straightforward process that provides insight into the effectiveness of your fulfillment operations. This metric reflects how well your process performs and can be used to enhance customer satisfaction and operational efficiency.
The formula for calculating order fulfillment rate is (Orders Shipped / Orders Received) x 100. For example, if 1,200 orders were placed and 1,029 orders were filled, the fulfillment rate would be (1,029 / 1,200) x 100, resulting in a fulfillment rate of 90.75%.
You can also calculate the order fulfillment rate based on cases or line items. For instance, if you're able to fulfill 3 out of 4 line items, your line count fill rate would be 75%.
To achieve greater levels of customer satisfaction and operational efficiency, companies can evaluate how well they are meeting consumer demand and pinpoint areas for improvement with the aid of accurate computation. The order fulfillment rate would be 95%, for instance, if a business completed 95 out of 100 orders that were received.
Here are the key factors to consider when calculating order fulfillment rate:
- Orders Shipped: The total number of orders that were successfully delivered to customers.
- Orders Received: The total number of orders that were placed by customers.
By regularly monitoring and analyzing your order fulfillment rate, you can identify areas for improvement and make data-driven decisions to optimize your fulfillment process.
Factors Affecting Order Fulfillment Rate
Effective inventory management is crucial for a high order fulfillment rate. Accurate stock levels and smart forecasting ensure item availability when orders arrive.
Several key factors influence order fulfillment rates, including inventory management, warehouse efficiency, and shipping partner reliability. Optimized storage systems and picking routes can significantly speed up order processing. Late deliveries or damaged goods can quickly decrease fulfillment rates.
Consider reading: Canada Lettermail Rates
Here are the key factors influencing order fulfillment rates:
- Inventory Management: Accurate stock levels and smart forecasting ensure item availability when orders arrive.
- Warehouse Efficiency: Optimized storage systems and picking routes can significantly speed up order processing.
- Shipping Partner Reliability: Late deliveries or damaged goods can quickly decrease fulfillment rates.
Addressing these factors can improve fulfillment performance and better meet customer demand.
Types of Fill
A high order fulfillment rate is a result of effective inventory management, which allows businesses to meet customer demand with the products they have in stock. This means maintaining sufficient inventory levels to promptly and fully satisfy customer orders.
There are several types of fill rates that businesses need to consider to assess their inventory management and supply chain effectiveness. Each type provides a distinct perspective on various elements of the fulfillment process.
A fill rate, or order fulfillment rate, is a percentage that measures how effectively a company can meet customer demand with the products it has in stock. A high fill rate indicates that a business is adept at maintaining sufficient inventory levels.
Low fulfillment rates can result in stockouts or delayed deliveries, leading to dissatisfied customers and potentially lost sales. Businesses must accurately forecast demand to maintain a high order fulfillment rate.
A business's supply chain operations' efficiency and ability to manage inventory effectively to meet fluctuating demand are reflected in its order fulfillment rate. This is crucial for building stronger relationships with customers by consistently meeting their expectations for product availability and delivery.
Factors Affecting
Effective inventory management is crucial to reducing stockouts and enhancing the fulfillment rate. This involves accurately tracking stock levels and using data analytics to improve forecasting and demand planning.
Accurate forecasting and demand planning can prevent inventory shortages, ensuring that orders are fulfilled promptly. By analyzing data, businesses can identify trends and patterns in customer behavior, making it easier to anticipate and meet demand.
Warehouse operations significantly impact the fulfillment rate, with optimized storage systems and picking routes helping to speed up order processing. This includes implementing efficient workflows and using technology to streamline tasks.
Supply chain efficiency is also vital, with vendor reliability and transportation effectiveness playing a significant role in the overall fulfillment rate. Businesses can improve supply chain efficiency by choosing reliable vendors and maintaining clear communication channels.
Here are the key factors influencing fulfillment:
- Inventory Management: Accurate stock levels and smart forecasting ensure item availability when orders arrive.
- Warehouse Efficiency: Optimized storage systems and picking routes can significantly speed up order processing.
- Shipping Partner Reliability: Late deliveries or damaged goods can quickly decrease fulfillment rates.
By addressing these factors, businesses can improve their fulfillment performance and better meet customer demand. This is essential for achieving customer satisfaction and optimizing inventory management.
Improving Order Fulfillment Rate
A high order fulfillment rate is crucial for meeting customer demand and earning their loyalty. If your fill rate is consistently low or dropping, you risk losing customers to competitors.
Inventory accuracy directly affects the fulfillment rate, so it's essential to maintain accurate records. Real-time inventory management systems provide current information on product availability, enhancing the speed and accuracy of order fulfillment.
Investing in advanced technology solutions, like warehouse management systems, can significantly improve fulfillment operations. These systems allow companies to adapt quickly to market changes, improving operational efficiency.
To avoid stockouts and overstocking, it's crucial to maintain an optimal inventory level. This can be achieved by implementing a safety stock policy and using inventory management software that provides real-time insights into inventory levels and demand forecasting recommendations.
Here are five key strategies to improve your order fulfillment rate:
- Optimize Inventory Levels: Maintain adequate stock levels to meet demand fluctuations without overstocking, ensuring timely order fulfillment.
- Improve Demand Forecasting: Use accurate data and forecasting techniques to anticipate customer demand patterns and adjust inventory accordingly.
- Enhance Supplier Relationships: Maintain strong partnerships with reliable suppliers to minimize lead times and ensure timely inventory replenishment.
- Streamline Order Processing: Implement efficient order processing systems and workflows to expedite order fulfillment and minimize errors.
- Invest in Technology: Use inventory management software and automation tools to track inventory levels in real-time, streamline operations, and improve overall efficiency.
By implementing these strategies, you can improve your order fulfillment rate, reduce errors, and increase customer satisfaction.
Challenges and Limitations
Maintaining a high fulfillment rate can be tough due to operational inefficiencies.
Supply chain disruptions are a major challenge, which can impact your ability to meet customer demand.
Technological limitations can also hinder your fulfillment performance, making it harder to keep up with orders.
Operational inefficiencies can lead to missed deadlines and disappointed customers, ultimately affecting your reputation.
Supply chain disruptions can be caused by various factors, including natural disasters, transportation issues, and supplier problems.
Addressing these challenges is crucial for maintaining customer satisfaction and meeting demand.
Overcoming Technological Limitations
Technological limitations can hinder maintaining a high fulfillment rate. Integrating automation and advanced software significantly increases fulfillment efficiency by reducing manual errors and speeding up processes.
Supply chain disruptions and technological limitations are common challenges that can impact your fulfillment performance. Operational inefficiencies can also cause problems.
Utilizing warehouse management systems for real-time tracking and better inventory management process streamlines order fulfillment. This allows businesses to tailor marketing strategies and enhance user experience.
A strategic approach to data analysis involves using technology and insights to drive better decisions and optimize fulfillment operations, enhancing customer satisfaction. Continuous monitoring and training ensure employees are proficient with new technologies, minimizing disruptions during transitions.
Here are some key technological solutions to overcome limitations:
- Warehouse management systems for real-time tracking and inventory management
- Inventory management software for tracking inventory levels in real-time
- Automation tools to streamline operations and improve efficiency
Unpredictable Trends
Unpredictable trends can cause chaos in the supply chain. A single viral post on social media can create a massive demand for a product almost overnight.
The COVID-19 pandemic is a prime example of this. A huge surge in personal protective equipment (PPE) left civilians scrambling to find masks and gloves.
Retailers wanted to stock up on masks quickly, but wholesalers that had them ran out fast, leaving them unable to fulfill orders. This was a totally unpredictable trend that caught everyone off guard.
Similar trends can blow up in many industries, causing order fill rates to decrease. This means that even with the best planning, businesses can still struggle to keep up with demand.
Tools and Software
Investing in advanced technology solutions like warehouse management systems can greatly enhance the efficiency of fulfillment operations.
Real-time data analysis from these systems allows companies to adapt quickly to market changes, improving operational efficiency. This is especially important for businesses that experience fluctuations in demand.
Efficient warehouse management software can optimize order-picking processes and layout for reduced travel distance, further enhancing fulfillment performance. By streamlining these processes, companies can reduce labor costs and improve customer satisfaction.
Effective inventory management is crucial for maintaining a high order fulfillment rate. Data analytics helps forecast customer demand, preventing stockouts and optimizing inventory levels.
Real-time visibility in inventory minimizes stock shortages and enhances order fulfillment. This is achieved through the integration of inventory management software that streamlines order processing and improves accuracy.
Investing in the right tools and software can make a significant difference in a company's order fulfillment rate. By leveraging technology to optimize operations, businesses can stay competitive and meet customer demands.
On a similar theme: Software Order Fulfillment
Data Analysis and Interpretation
Data analysis is key to understanding your order fulfillment rate. By analyzing customer behavior and operational data, businesses can tailor marketing strategies and enhance user experience.
A strategic approach to data analysis involves using technology and insights to drive better decisions and optimize fulfillment operations, enhancing customer satisfaction.
Calculating fill rate helps identify opportunities for improvement in the fulfillment process, leading to better operational efficiency.
Analyzing trends over time and identifying patterns is crucial in pinpointing areas for improvement in your fulfillment process.
A high order fulfillment rate indicates efficient operations and satisfied customers, but don't focus solely on the number.
Best Practices and Tips
To increase your order fulfillment rate, it's essential to optimize your inventory levels. Maintain adequate stock levels to meet demand fluctuations without overstocking, ensuring timely order fulfillment.
Improving demand forecasting is crucial for anticipating customer demand patterns and adjusting inventory accordingly. Use accurate data and forecasting techniques to stay ahead of the game.
Strong supplier relationships are vital for minimizing lead times and ensuring timely inventory replenishment. Maintain partnerships with reliable suppliers to keep your inventory levels on track.
Streamlining order processing is key to expediting order fulfillment and minimizing errors. Implement efficient order processing systems and workflows to get orders out the door quickly.
Investing in technology can greatly improve your order fulfillment rate. Use inventory management software and automation tools to track inventory levels in real-time and streamline operations.
Here are the five key tips for raising your order fulfillment rate at a glance:
- Optimize Inventory Levels
- Improve Demand Forecasting
- Enhance Supplier Relationships
- Streamline Order Processing
- Invest in Technology
Frequently Asked Questions
What does order fulfillment mean?
Order fulfillment is the process of receiving, processing, and delivering customer orders, from initial purchase to final delivery. It also includes managing returns and exchanges, ensuring a smooth and efficient customer experience.
Sources
- https://ordersinseconds.com/optimize-your-order-fulfillment-rate/
- https://dclcorp.com/blog/fulfillment/perfect-order-rate/
- https://www.warehousingandfulfillment.com/warehousing-and-fulfillment-resources/the-importance-of-fill-rate-in-supply-chain-management/
- https://seller.alibaba.com/businessblogs/what-is-order-fill-rate-and-why-is-it-important-for-wholesalers-pxno4212
- https://www.linkedin.com/pulse/how-calculate-order-fulfillment-rate-osequip-klaje
Featured Images: pexels.com