
An order fulfillment process flow chart is a visual representation of the steps involved in processing orders from start to finish. It helps businesses streamline their operations and ensure timely delivery of products to customers.
The flow chart typically begins with the receipt of an order, which is then verified for accuracy. According to the article, the next step is to check inventory levels to ensure that the ordered products are in stock.
A well-designed flow chart should also include a section for order processing, where orders are assigned to specific fulfillment teams or warehouses. This helps to ensure that orders are processed efficiently and effectively.
By following a standardized process flow chart, businesses can reduce errors and improve customer satisfaction.
Benefits and Objectives
The primary objective of an optimized order fulfillment process is to ensure speed and accuracy in order processing. This leads to a more efficient supply chain and improved customer satisfaction.
Order fulfillment is crucial for businesses as it increases customer satisfaction, drives repeat business, and stimulates growth through positive word of mouth. This, in turn, improves customer retention and brand loyalty.
A well-implemented order fulfillment process can also boost sales and revenue by reducing labor, inventory management, and shipping costs, as well as faster turnaround times.
Objectives of an Optimized
The primary objective of an optimized order fulfillment process is to ensure speed and accuracy in order processing. This can be achieved by streamlining supply chains and reducing fulfillment challenges.
Minimizing errors and delays is another key objective of an optimized order fulfillment process. By doing so, businesses can improve customer satisfaction.
Enhancing the overall customer experience is a top priority for businesses that want to optimize their order fulfillment process. This can be done by implementing efficient workflows and utilizing flow charts.
By achieving these objectives, businesses can improve their customer satisfaction rates and stay competitive in the market.
Importance of Importance for Businesses
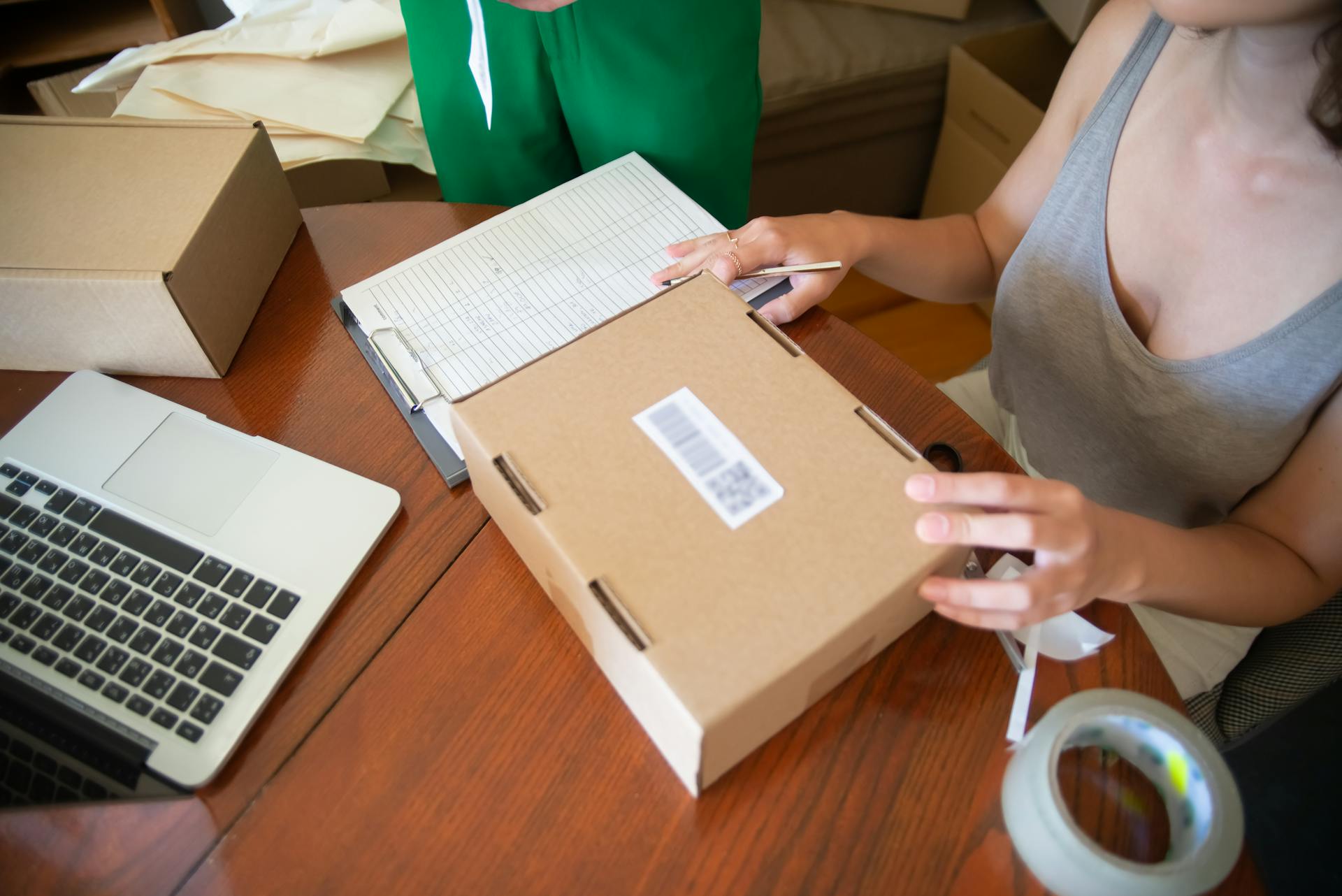
Investing in order fulfillment is crucial for businesses across industries. It's a key factor in increasing customer satisfaction, which in turn drives repeat business and stimulates growth through positive word of mouth.
Order fulfillment plays a significant role in reducing order processing time, leading to more timely deliveries. This not only boosts sales and revenue but also reduces labor, inventory management, and shipping costs.
By implementing efficient workflows, businesses can achieve faster turnaround times. This is a major advantage, as it allows companies to stay competitive in the market and retain customers.
Here are some key benefits of effective order fulfillment:
- Increases customer satisfaction, drives repeat business, and stimulates growth through positive word of mouth
- Boosts sales and revenue by reducing labor, inventory management, and shipping costs
- Reduces order processing time, leading to more timely deliveries
Key Components
When creating an order fulfillment process flow chart, it's essential to understand the key components involved.
The first key component is order entry and validation, which sets the stage for the entire process.
Order entry and validation is followed by inventory management, which ensures that the necessary items are available for shipping.
Quality control is another crucial component, as it guarantees that products meet the required standards before they're shipped out.
Key Components
Order fulfillment is a complex process that involves several key components.
The first stage of order fulfillment is order entry and validation, where customer orders are received and verified for accuracy.
Inventory management is a crucial component of order fulfillment, ensuring that products are available to meet customer demand.
Picking and packing are critical stages in the process, where products are selected and packaged for shipping.
Shipping is the stage where orders are dispatched to customers, often involving logistics and transportation services.
Quality control is also a key component, ensuring that products meet quality standards before they are shipped.
Delivery is the final stage, where products are received by customers, and returns and exchange management is the process of handling customer returns and exchanges.
Inventory Management & Availability
Inventory management and product availability are crucial components of a smooth order fulfillment process. Identifying key stages and activities involved in the process, such as inventory management, is essential for businesses to understand the flow of their order fulfillment process.
Inventory management involves monitoring inventory levels, restocking when necessary, and managing SKU information. This step is critical to ensure that ordered products are in stock and available for fulfillment.
Businesses should also ensure that their warehouse layout is optimized to improve fulfillment speed and accuracy. Items with high-turnover rates should be stored close to the fulfillment areas, whereas less popular products should remain in the back of the warehouse.
Separating product variances by SKUs can also reduce picking inaccuracies. This helps employees quickly locate the correct products and reduces errors.
By implementing a process flow chart, businesses gain improved visibility and control over their order fulfillment process. They can track orders at each stage, identify bottlenecks, and make necessary adjustments to ensure efficient and timely order processing.
Inventory software collects data from each transaction to generate detailed reports. This information enables management to improve their order fulfillment strategies to improve efficiency, accuracy, and speed.
Order Fulfillment Process
The order fulfillment process involves several stages, each with its own unique steps. Here's a brief overview of what happens at each stage.
Order entry and validation is the first stage, where businesses receive an order from a customer and verify the details. This stage is crucial in ensuring that the order is accurate and can be fulfilled.
Receiving is the next stage, where incoming inventory is accepted and audited to ensure all products are present and intact. Any damaged items should be returned immediately.
Picking, packing, and shipping is the final stage, where the ordered products are retrieved, packed securely, and prepared for shipment. This can be done by a dedicated picking team or automated systems to expedite the process.
Entry
The entry stage of the order fulfillment process is where everything starts. This is where businesses receive an order from a customer.
To begin, businesses need to capture relevant customer information, such as their name and contact details.
Next, they must verify the order details to ensure they're accurate and complete. This is crucial to prevent errors and misunderstandings later on.
The order entry stage also involves checking for availability of the requested products.
Order Fulfillment
Order fulfillment is the process of getting products to customers after they've placed an order. It officially begins when a customer places an order, and pickers are automatically alerted with every request.
The picking stage involves selecting the quantity of items from inventory, which can be done through piece picking, zone picking, or batch picking. Piece picking collects the products one order at a time, while zone picking assigns each picker to a specific warehouse zone. Batch picking, on the other hand, involves pickers collecting products for several orders at once.
The order processing workflow involves four stages: picking, sorting, packing, and shipping. Picking is the most critical stage, as it determines the accuracy of the order. Sorting separates picked items according to their destination, which is essential for accurate delivery and customer satisfaction.
Packing involves not just putting items in boxes to ship, but also making sure it's the right box and the item is protected throughout delivery. This includes weighing the package, labeling it, and adding any shipping instructions. The type of packing materials used depends on the company's weight limit for standard packages.
In some cases, businesses print off an invoice that outlines the order before sealing the box with packing tape. Depending on the type of inventory, employees may use bubble wrap, tissue paper, or packing peanuts to wrap the products and ensure they aren't damaged during transportation.
The shipping stage involves transporting orders to their destination, whether directly to the customer or consolidated with other orders going to nearby locations to save money. This can be done through automated systems to expedite the process.
Here are the four stages of the order processing workflow:
Receive
Receiving is a critical step in the order fulfillment process, where incoming inventory is accepted and processed for stocking.
Each shipment must be audited, recorded, and stocked to ensure the product picking crew can begin fulfilling orders. This involves cross-examining the physical units with the purchase order, invoice, and shipping list to ensure all products are present and intact.
Damaged items should be returned immediately for a refund or credit to avoid any losses. This process helps maintain accurate inventory levels and prevents any potential issues downstream.
New SKU barcodes should be created and implemented into the management system as soon as possible to ensure accurate tracking and inventory management.
Process Flow
Identifying key stages and activities is crucial in creating an order fulfillment process flow chart. These stages may include order entry and validation, inventory management, picking, packing, shipping, quality control, delivery, and returns and exchange management.
By mapping out the sequential flow of activities, businesses can identify potential bottlenecks and optimize the flow to improve efficiency. This involves determining the order in which each activity occurs and visualizing the flow from one stage to another.
Having a clear plan and schedule in place is essential to stay on schedule. This can be achieved by using powerful Gantt charts that organize production phases, link task dependencies, and filter for the critical path to identify essential tasks.
Plan, Schedule, Track Production Steps
Creating a production plan is crucial to ensure a smooth order fulfillment process. By planning, scheduling, and tracking each step of the production process, businesses can avoid costly delays and stay on schedule.
Gantt charts are a powerful tool for organizing production phases and linking task dependencies. This allows businesses to identify the critical path and focus on essential tasks that need to be completed for the production to be successful.
Having a baseline plan is essential to capture the production plan and compare it in real-time to actual progress. This helps businesses stay on schedule and make adjustments as needed.
Identifying key stages and activities in the production process is the first step in creating a production plan. These stages may include creating products to stock, packaging, and shipping, and inventory management.
Including decision points and alternative paths in the production plan allows for flexibility in handling exceptions or variations in the process. This can include rush orders or customizations that require special handling.
By mapping out the sequential flow of activities, businesses can identify potential bottlenecks and optimize the flow to improve efficiency. This is especially important in the production process where delays can have a significant impact on the entire order fulfillment process.
Delivery and Tracking
Delivery and tracking is a crucial stage in the process flow, where products are handed over to the chosen transportation channel for delivery.
Once products are packed and ready for shipment, they are handed over to the chosen transportation channel for delivery. This stage involves coordinating with logistics providers, selecting the most suitable carrier, and generating tracking information to enable customers to track their orders.
Coordinating with logistics providers is essential to ensure smooth delivery.
The most suitable carrier is selected based on the product's size, weight, and destination.
Streamlining and Automation
Streamlining and automation are key components of an efficient order fulfillment process. By using workflows and flow charts, businesses can facilitate streamlined communication and collaboration among teams and departments involved in the process.
Clear guidelines and responsibilities outlined in the flow chart help eliminate confusion and enhance coordination, leading to more efficient operations. This is especially true when integrating technology and automation, which can significantly enhance the efficiency and accuracy of the order fulfillment process.
With modern software, most stages of the fulfillment process can be automated, including inventory ordering and picking list generation.
Streamlined Communication
Streamlined communication is key to efficient order fulfillment. Clear guidelines and responsibilities outlined in flow charts help eliminate confusion and enhance coordination.
Having a clear communication channel can make all the difference in a busy order fulfillment process. This is especially true when different teams and departments are involved.
Flow charts can be a game-changer in this regard, as they provide a visual representation of the order fulfillment process. This helps teams stay on the same page and work together seamlessly.
By implementing a streamlined communication system, businesses can reduce errors and improve overall efficiency. This is a crucial step in streamlining and automating the order fulfillment process.
Automate
Automating the order fulfillment process can significantly enhance efficiency and accuracy. Technology and automation can minimize errors, streamline operations, and expedite order processing.
Modern software can automate most stages of the fulfillment process, including inventory ordering and picking list generation. This can save time and reduce manual errors.
Automation can be achieved through integration with an order management system, inventory management software, and automated picking and packing systems. This can help businesses streamline operations and improve service speed and accuracy.
Here are some examples of automated processes in order fulfillment:
- Inventory ordering
- Picking list generation
Using project management software like ProjectManager can also help automate order fulfillment workflows. Its collaborative features and powerful kanban boards can track inventory, sorting, packing, and shipping.
Third-Party Services
Third-Party Services can be a game-changer for growing businesses, allowing them to focus on making their products while leaving order fulfillment to the experts.
One of the biggest advantages of using a third-party service is that it saves the vendor from having to hire seasonal logistic staff for busy periods.
This can lead to faster fulfillment and localizes inventory closer to customers, making it a win-win for both the vendor and the customer.
Stages of the Process
The order fulfillment process has several key stages that work together to get products from a warehouse to a customer's doorstep. Identifying these stages is crucial for creating an effective order fulfillment process flow chart.
Order fulfillment involves many moving parts, including order entry and validation, inventory management, picking, packing, shipping, quality control, delivery, and returns and exchange management.
To break it down further, there are four main steps in the order processing stage: picking, sorting, packing, and shipping. Here's a brief overview of each:
Stages of the
The order fulfillment process has many moving parts that work simultaneously, requiring businesses to implement an organized strategy to ensure each stage is performed accurately and efficiently.
To understand the order fulfillment process, let's break it down into its key stages. These stages may include order entry and validation, inventory management, picking, packing, shipping, quality control, delivery, and returns and exchange management.
Order processing is a crucial stage in the order fulfillment process, involving four key steps: picking, sorting, packing, and shipping.
Picking is the first step in order processing, and it involves selecting the quantity of items from inventory. There are three types of picking methods: piece picking, zone picking, and batch picking.
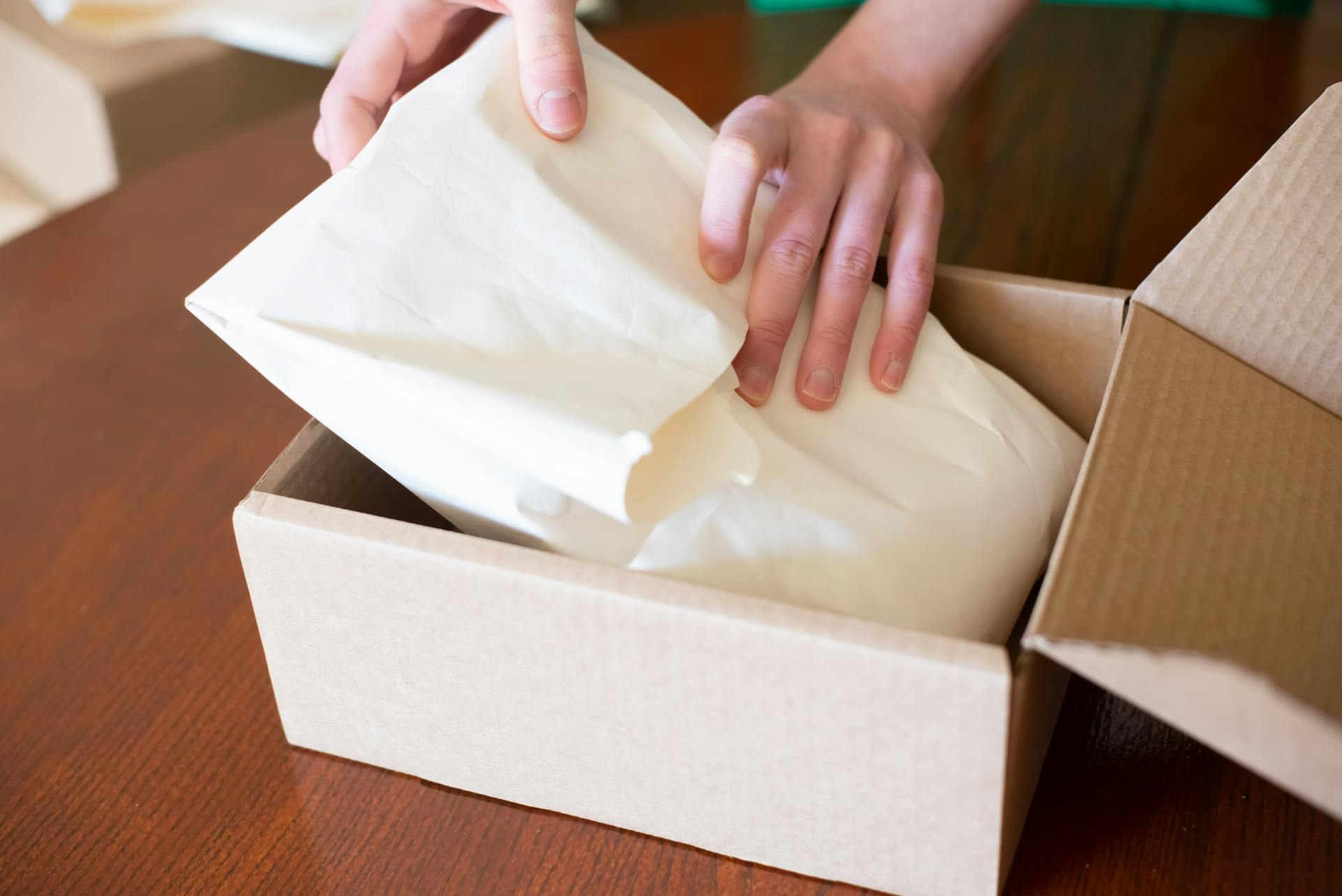
Sorting is an essential step in order processing, and it involves separating picked items according to their destination. This step is crucial for accurate delivery and customer satisfaction.
Packing is not just about putting items in boxes to ship, but also about making sure it's the right box and the item is protected throughout delivery. This includes weighing the package, labeling it, and adding any shipping instructions.
Shipping is the final step in order processing, and it involves transporting orders to their destination.
Returns
Returns are a necessary part of the retail process, and businesses need to have a clear plan in place to handle them.
All retailers will experience a return for one reason or another, so it's essential to implement a comprehensive return policy that clarifies how and when customers can initiate the return process.
Companies also need to implement a process to accept returning products and reintroduce them back into inventory.
A return policy should outline the steps customers need to take to initiate the return process, including any necessary documentation or communication with the retailer.
Businesses should have a system in place to efficiently process returns and restock inventory, reducing waste and minimizing the impact on operations.
Technology and Tools
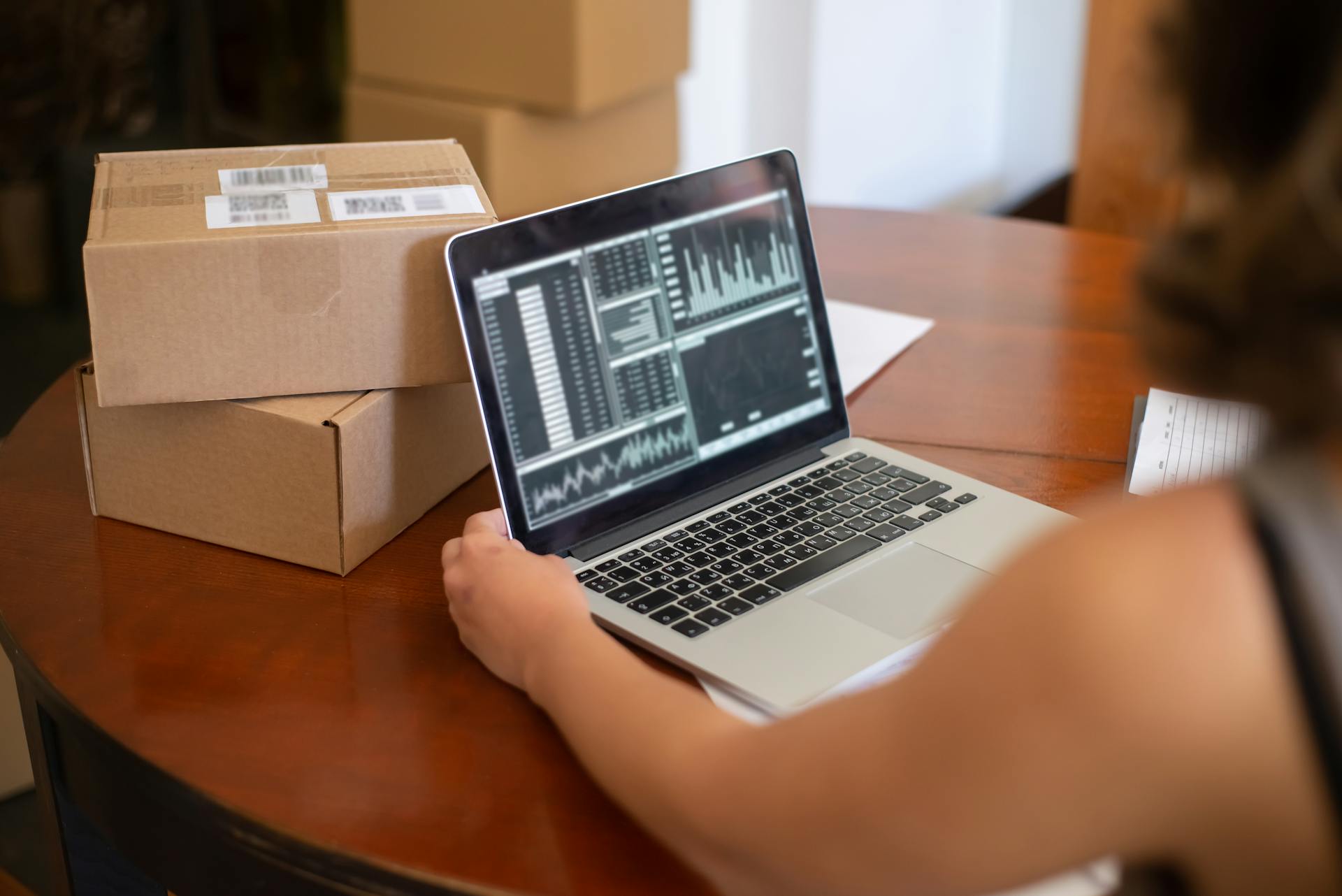
Incorporating technology and automation can significantly enhance the efficiency and accuracy of the order fulfillment process.
Technology can minimize errors and streamline operations by integrating an order management system, inventory management software, and automated picking and packing systems.
Automated systems can expedite order processing, making it faster and more reliable.
Integration of these systems can help businesses stay competitive in today's fast-paced market.
Best Practices and Considerations
When implementing an order fulfillment process flow chart, it's essential to consider the accuracy of product information. This includes ensuring that product details, such as weights and dimensions, are up-to-date and accurate.
To avoid delays, it's crucial to have a clear understanding of the shipping options available. This includes knowing the estimated delivery times for each shipping method and the associated costs.
A well-designed order fulfillment process flow chart should also take into account the need for regular inventory updates. This will help prevent stockouts and ensure that products are always available for shipping.
Quality Control
Quality Control is a crucial step in ensuring customer satisfaction and minimizing returns. This stage involves performing quality control checks to verify that products meet the required standards.
To maintain customer satisfaction, quality control checks should be performed. Any damaged goods or quality issues are identified and addressed appropriately. This helps to prevent unhappy customers and costly returns.
Quality control checks ensure that products are in good condition and ready for shipment. This is essential for maintaining a positive reputation and building trust with customers.
Strategy Considerations
Developing a solid strategy is crucial for effective order fulfillment. Order fulfillment looks slightly different for every organization, as they may handle diverse inventory, clients, and order volumes.
As you tailor your strategy, consider the unique needs of your business. Every organization has its own strengths and weaknesses, and a one-size-fits-all approach won't cut it.
Inventory management is key to successful order fulfillment. Diverse inventory requires careful planning and organization to ensure timely and accurate order processing.
Client needs and preferences also play a significant role in determining your order fulfillment strategy. Understanding their expectations and requirements will help you provide the best possible service.
Order volumes can fluctuate, and a flexible strategy is necessary to accommodate changes in demand. This might involve adjusting inventory levels, staffing, or logistics to meet new requirements.
Ultimately, a well-designed strategy will help you navigate the complexities of order fulfillment and set your business up for success.
Frequently Asked Questions
What is the lifecycle of an order fulfillment process begins?
The order fulfillment process begins when a customer places an order. It then flows through a series of steps to ensure timely delivery and customer satisfaction.
What are the steps for maximizing order fulfillment?
Maximize order fulfillment by automating processes, optimizing inventory management, and streamlining returns and shipping to ensure efficient and transparent order fulfillment
Sources
- https://online.visual-paradigm.com/diagrams/templates/flowchart/order-fulfillment-flowchart-
- https://www.servicefolder.com/resources/field-service-management-blog/Optimizing_Your_Business_with_an_Order_Fulfillment_Process_Flow_Chart.html
- https://zipordering.com/order-fulfillment.html
- https://www.slidegeeks.com/powerpoint/Order-Fulfillment-Process
- https://www.projectmanager.com/blog/order-fulfillment
Featured Images: pexels.com