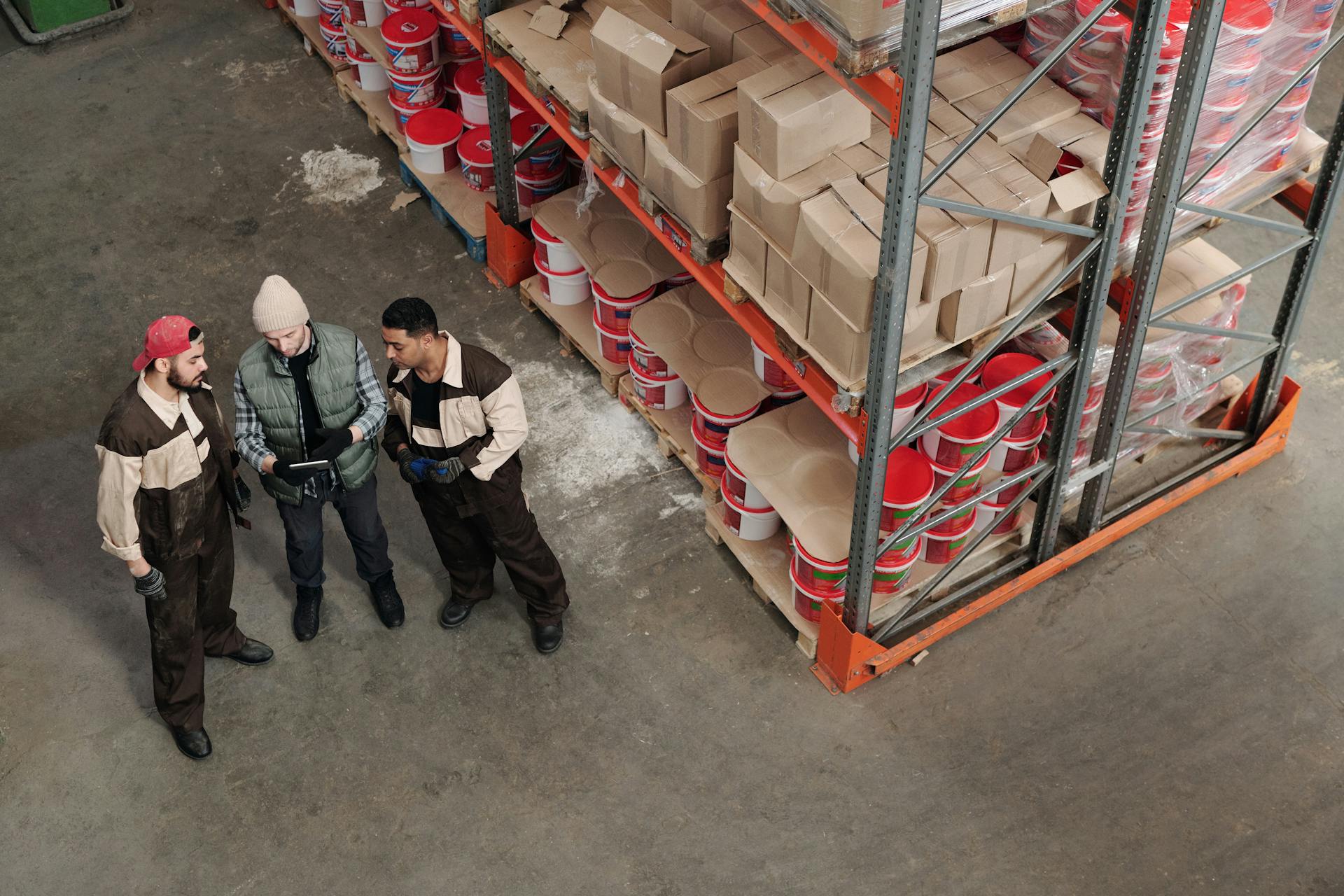
Order fulfillment cycle time is a critical metric that affects every business, big or small. It's the time it takes to get an order from a customer to their doorstep, and it's a key driver of customer satisfaction and loyalty.
The average order fulfillment cycle time is around 10-14 days, but it can vary significantly depending on the industry and business model. In e-commerce, for example, cycle times can be as short as 2-3 days, while in traditional retail, it can take up to 30 days or more.
Understanding the components of the order fulfillment cycle time is essential to optimizing it. This includes the time it takes to pick, pack, and ship orders, as well as the time it takes for payment processing and inventory replenishment.
What Is
Order fulfillment cycle time is the amount of time it takes to get an order from a customer to their doorstep. This includes the time it takes to process the order, pick and pack the items, and ship them to the customer.
The average order fulfillment cycle time is around 5-7 days, but this can vary depending on the complexity of the order and the efficiency of the fulfillment process.
A well-optimized fulfillment process can reduce cycle time by up to 30%, resulting in faster delivery times and increased customer satisfaction.
Measuring OFCT
You can use an order fulfillment cycle time formula to guide you when measuring fulfillment in your business. The most commonly seen formula works out the sum of the entire production and delivery time.
There are several ways to measure OFCT, including:
- Promised Customer Order Cycle Time – This is the expected order fulfillment time that you tell your customers.
- Actual Customer Order Cycle Time – This is the average time it takes for a customer to receive a product after ordering it.
- Cash to Cash Cycle Time – The time taken from spending money on raw materials and supplies to when you receive money from them as finished goods.
- Supply Chain Cycle Time – How long it takes to fulfill a customer order if the requisite raw materials are at zero.
Each of these metrics has value when analyzing your business’ order fulfillment and supply chain capacities.
Gauging Customer Satisfaction
A short order cycle time is essential for delivering a seamless fulfillment experience, which can contribute to higher customer satisfaction levels. This is because a short cycle time enables you to offer faster shipping options, such as 2-day shipping.
A long order cycle time, on the other hand, can result in fulfillment delays and longer delivery times, which will translate to more dissatisfied customers. This is especially true for online shoppers, who expect a quick turnaround time.
The closer the delivery date is to the order date, the better the customer experience. This is a key factor in gauging customer satisfaction, and it's something you can measure and improve upon.
By optimizing your supply chain and choosing reliable shipping partners, you can reduce your order fulfillment cycle time and improve customer satisfaction. This is a win-win situation for both you and your customers.
Measuring
Measuring OFCT involves tracking various metrics to understand the effectiveness of your order fulfillment process. You can use an order fulfillment cycle time formula to guide you in measuring fulfillment in your business.
The most commonly seen formula works out the sum of the entire production and delivery time. This includes the time it takes for your team to receive a manufacturing order, start the manufacturing process, assemble, finish, and pack the order, and then deliver it to the customer.
You should track four key metrics: Promised Customer Order Cycle Time, Actual Customer Order Cycle Time, Cash to Cash Cycle Time, and Supply Chain Cycle Time. These metrics help you understand the different stages of the order fulfillment process and identify areas for improvement.
To measure OFCT, you can use the following formula:
- Promised Customer Order Cycle Time: the expected order fulfillment time you tell your customers
- Actual Customer Order Cycle Time: the average time it takes for a customer to receive a product after ordering it
- Cash to Cash Cycle Time: the time taken from spending money on raw materials and supplies to when you receive money from them as finished goods
- Supply Chain Cycle Time: how long it takes to fulfill a customer order if the requisite raw materials are at zero
These metrics can fluctuate over time due to changes or disruptions in the supply chain. You should constantly monitor and reassess your order cycle time to determine whether you need to review your supply chain processes and make improvements that will speed up the process.
By tracking these metrics and using the order fulfillment cycle time formula, you can gain a better understanding of your order fulfillment process and make data-driven decisions to improve it.
Calculating OFCT
Calculating order fulfillment cycle time (OFCT) is crucial for businesses to track their effectiveness in fulfilling customer orders. You can use a simple formula to find your average delivery timeline.
The order fulfillment cycle time formula is: Sourcing time + Production time + Delivery time = Order fulfillment cycle time (OFCT). This formula helps you understand the different stages involved in fulfilling a customer order.
To calculate OFCT, you need to track three key phases: sourcing time, production time, and delivery time. Sourcing time is the duration between a customer's order and when you gather all necessary materials. If you have the product in stock, there's no sourcing time.
Production time, also called packing time, covers retrieving the product, quality inspection, and packaging it for shipment. Delivery time starts when your shipping team completes packaging and ends when the product reaches the customer.
Here's an example of how to calculate OFCT using the formula: A customer orders your product on July 15. Since you have it in stock at a fulfillment center in their region, there's no sourcing time. Your warehouse packages it that afternoon (packing time) and ships it the next day. The customer receives it on July 19 (delivery time), making the total fulfillment time four days.
The order cycle time formula is: (Delivery Date – Order Date) / Total Orders Shipped. This formula helps you calculate the average time it takes for a customer to receive a product after ordering it.
Here are the different metrics to measure OFCT:
Each of these metrics has value when analyzing your business' order fulfillment and supply chain capacities.
Ways to Improve
Improving order fulfillment cycle time requires a multifaceted approach. Here are some effective ways to achieve this:
Optimizing warehouse flow is essential to reducing order cycle time. By streamlining warehouse operations, you can minimize bottlenecks and improve picking efficiency. For instance, measuring warehouse KPIs and optimizing warehouse setup can help reduce order cycle time.
Inventory optimization is also crucial in improving order cycle time. Maintaining the right inventory balance is vital – too much inventory can tie up capital and space, while too little can lead to delays. Inventory control software and data analytics can help you strike the perfect balance.
Efficient warehouse management is at the heart of quick order fulfillment. Consider optimizing your warehouse layout to expedite the picking, packing, and shipping process. Place frequently picked items closer to the packing area to minimize travel time.
Route optimization is a game-changer for order cycle time reduction. Leveraging route planning software allows you to identify the most efficient delivery routes, minimizing travel time and reducing fuel costs.
Streamlining order processing involves simplifying and optimizing the steps from order receipt to order validation. Implementing automated order processing systems can significantly expedite this crucial phase, reducing reliance on manual data entry and minimizing errors.
Reducing putaway time is another key strategy to improve order fulfillment cycle time. The quicker your warehouse can move inbound shipments from the receiving dock to ready-to-pick on the shelf, the fewer delays you'll have in your order fulfillment process.
Setting protocols and limits is essential to improving the fulfillment process. Limiting picking batch size, setting up guidelines for returned items, and establishing limits on inventory reorders can all help avoid stockouts and backorders, which can slow down your order cycle time.
Here are some specific strategies to improve order fulfillment cycle time:
• Implement automated order processing systems
• Optimize warehouse layout to expedite the picking, packing, and shipping process
• Leverage route planning software for efficient delivery routes
• Reduce putaway time by moving inbound shipments quickly
• Set protocols and limits to avoid stockouts and backorders
OFCT Benefits
Improving your Order Fulfillment Cycle Time (OFCT) can have a significant impact on your business. Faster deliveries can boost customer satisfaction, with online shopping data showing that satisfaction is largely tied up in fast deliveries.
Customers can be very picky when it comes to their online shopping, and a fast delivery is often a key factor in their satisfaction. By reducing your OFCT, you can improve customer satisfaction and increase customer loyalty.
Here are the benefits of improving your OFCT:
Faster fulfillment times offer several key advantages, including improved customer satisfaction, increased customer loyalty, and enhanced operational efficiency. By reducing your OFCT, you can stay ahead in the race and improve your overall business performance.
OFCT Optimization
Optimizing your Order Fulfillment Cycle Time (OFCT) is crucial for any e-commerce business. Customer satisfaction is largely tied up in fast deliveries, so it's essential to track and reduce your OFCT.
The life cycle of order fulfillment encompasses many steps, from receiving a customer order to delivering it. This cycle can take days or even weeks, but you can control the OFCT in the supply-chain and manufacturing sides of your business.
To get your OFCT as low as possible, start by measuring your warehouse KPIs and looking for opportunities to make improvements. This can include optimizing your warehouse setup and using warehouse slotting to make the most of available space and improve picking efficiency.
Here are some ways to reduce your OFCT:
- Improve your warehouse flow by identifying bottlenecks and optimizing your warehouse setup.
- Optimize your inventory levels by using inventory control software and data analytics to predict demand and monitor stock levels in real-time.
- Use efficient picking methods, such as batch picking or wave picking, to reduce order fulfillment cycle time.
- Consider using a 3PL like Red Stag Fulfillment to design a process that gives you the most efficient order cycle time.
By implementing these strategies, you can reduce your OFCT and improve customer satisfaction. Remember, it's essential to track and analyze your OFCT to identify areas for improvement and optimize your logistics systems.
OFCT Efficiency
Understanding OFCT efficiency is crucial to streamlining your order fulfillment process. It's essential to track your average OFCT to ensure customer satisfaction, as online shopping consumer data shows that fast deliveries are a top priority.
Customer satisfaction is largely tied up in fast deliveries, so it's no surprise that OFCT is a vital metric for businesses to track. By keeping your average OFCT low, you can increase customer satisfaction and loyalty.
There are several ways to measure OFCT, including Promised Customer Order Cycle Time, Actual Customer Order Cycle Time, Cash to Cash Cycle Time, and Supply Chain Cycle Time. Each of these metrics provides valuable insights into your order fulfillment process.
To reduce your Actual Customer Order Cycle Time, you can optimize your warehouse layout to expedite the picking, packing, and shipping process. This can be done by placing frequently picked items closer to the packing area to minimize travel time.
Here are some ways to improve OFCT efficiency:
- Promised Customer Order Cycle Time: 3-5 days
- Actual Customer Order Cycle Time: 5-7 days
- Cash to Cash Cycle Time: 30-60 days
- Supply Chain Cycle Time: 7-14 days
By streamlining your order fulfillment process, you can reduce your OFCT and improve customer satisfaction. Remember, efficient warehouse management is at the heart of quick order fulfillment, so be sure to optimize your warehouse layout and processes to get orders out the door quickly.
OFCT Technology
Understanding OFCT Technology is crucial to streamlining your order fulfillment process. By adopting advanced order management software, you can identify bottlenecks and automate routine tasks.
This technology provides a comprehensive view of your entire order cycle, allowing you to make data-driven decisions. Supply chain digitization can also provide real-time insights into inventory levels, order status, and delivery tracking.
Investing in the right technology can reduce manual work and improve overall efficiency. OFCT can be affected by external factors, but you can control it in the supply-chain and manufacturing sides of your business.
To get the most out of OFCT technology, consider the following metrics:
OFCT Logistics
Order fulfillment cycle time (OFCT) is a crucial metric for businesses to track, as it directly affects customer satisfaction. Customer satisfaction is largely tied up in fast deliveries, and customers can be very picky when it comes to their online shopping.
The life cycle of order fulfillment encompasses many steps, including receiving a customer order, placing a manufacturing order, assembling, finishing, and packing the order, and delivering it to the customer. This process can take days or even weeks, and is affected by external factors like shipping overseas.
To reduce OFCT, you can control the supply-chain and manufacturing sides of your business. This involves streamlining your order fulfillment cycle to lower your average OFCT. As your business grows, managing OFCT gets more complicated, as order fulfillment becomes dependent on many entities in your business.
There are several ways to measure OFCT, including:
- Promised Customer Order Cycle Time: the expected order fulfillment time you tell your customers
- Actual Customer Order Cycle Time: the average time it takes for a customer to receive a product after ordering it
- Cash to Cash Cycle Time: the time taken from spending money on raw materials and supplies to when you receive money from them as finished goods
- Supply Chain Cycle Time: the order fulfillment cycle time plus the time it takes to order and receive supplies
Each of these metrics has value when analyzing your business' order fulfillment and supply chain capacities. By understanding and tracking these metrics, you can identify areas for improvement and optimize your order fulfillment process.
To further reduce OFCT, consider outsourcing your fulfillment to a 3PL dedicated to providing order fulfillment services. This can help you reduce your cycle time while improving fulfillment accuracy.
Setting clear protocols and procedures is also essential to improving the order fulfillment process. This includes limiting picking batch size, setting up guidelines for returned items, and establishing protocols for handling late deliveries.
Optimized inventory and order management is also key to reducing OFCT. This involves using proprietary software to efficiently manage your orders and inventory, and providing real-time updates on inventory levels.
Efficient warehouse management is at the heart of quick order fulfillment. This includes optimizing your warehouse layout to expedite the picking, packing, and shipping process, and implementing modern supply chain services technology like barcode scanners to improve accuracy and speed.
Implementing multi-carrier parcel management can also help reduce OFCT by picking the best carrier for each package. This can result in faster delivery times and cost savings.
OFCT Warehouse
Improving warehouse flow is crucial to reducing order cycle time. Bottlenecks in the warehouse can slow down the picking and packing process, making it harder to get orders out the door quickly.
By identifying and addressing inefficiencies, you can optimize your warehouse setup and improve picking efficiency. This includes ensuring pickers can find items easily and that shelving racks are properly spaced out.
Optimizing warehouse flow also involves using warehouse slotting to make the most of available space. This can help reduce order cycle time and keep your warehouse running smoothly.
Efficient Warehouse Management
Efficient Warehouse Management is crucial for quick order fulfillment. It requires optimizing your warehouse layout to expedite the picking, packing, and shipping process. By placing frequently picked items closer to the packing area, you can minimize travel time.
You can significantly reduce the time it takes to get orders out the door by reimagining your warehouse's layout and processes. Implement modern supply chain services technology like barcode scanners to improve accuracy and speed when processing orders.
To improve picking efficiency, you may need to optimize your warehouse setup and use warehouse slotting to make the most of available space. Measuring your warehouse KPIs can help you identify opportunities for improvement.
Here are some key warehouse layout considerations to keep in mind:
By addressing these warehouse layout considerations, you can improve your order cycle time and increase customer satisfaction.
Warehouse Locations
Our OFCT Warehouse locations are strategically placed to provide efficient fulfillment services to customers on both coasts.
We have a dedicated East Coast fulfillment services & 3PL warehouse, which allows us to quickly and accurately process orders for customers in the eastern United States.
On the West Coast, we have a similarly equipped warehouse that enables us to provide fast and reliable fulfillment services to customers on the West Coast.
We've carefully selected the best 3PL companies to partner with, ensuring that our customers receive the highest level of service and support.
Our East Coast warehouse is a hub for our East Coast operations, offering a wide range of services, including order fulfillment, inventory management, and shipping.
Our West Coast warehouse is designed to meet the unique needs of our West Coast customers, with services tailored to their specific requirements.
By partnering with top 3PL companies, we're able to leverage their expertise and resources to provide our customers with the best possible service.
OFCT Supply Chain
The order fulfillment cycle time (OFCT) supply chain is a critical component of any business, as it directly affects customer satisfaction and overall operational efficiency.
A long order cycle time is an indicator that you need to review your supply chain process to identify any inefficiencies or unnecessary steps that need to be optimized or removed entirely.
Knowing your business’s order cycle time can help detect issues in the supply chain that could be causing delays in your order fulfillment process.
Here are some key metrics to track in your OFCT supply chain:
- Promised Customer Order Cycle Time – This is the expected order fulfillment time that you tell your customers.
- Actual Customer Order Cycle Time – This is the average time it takes for a customer to receive a product after ordering it.
- Cash to Cash Cycle Time – The time taken from spending money on raw materials and supplies to when you receive money from them as finished goods.
- Supply Chain Cycle Time – How long it takes to fulfill a customer order if the requisite raw materials are at zero.
Each of these metrics has value when analyzing your business’s order fulfillment and supply chain capacities.
Supplier collaboration is also essential in optimizing your OFCT supply chain. When suppliers understand your needs and preferences, they can work more efficiently to fulfill orders promptly.
Having visibility into every element of your supply chain allows you to spot potential problems and act to head them off. Understanding the lead time for sourcing raw materials, manufacturing finished goods, and transporting them from the factory to the 3PL will help you run a supply chain that is both lean and able to deliver the products you need at the right times.
By optimizing your OFCT supply chain, you can significantly reduce the time it takes to get orders out the door and improve customer satisfaction.
OFCT Improvement
Improving your Order Fulfillment Cycle Time (OFCT) requires a combination of understanding the process and making strategic changes.
The OFCT encompasses many steps from receiving a customer order to the completed delivery. It's essential to track this metric to ensure customer satisfaction, as fast deliveries are crucial for online shopping.
To improve OFCT, you need to optimize different aspects of your supply chain processes. This includes streamlining communication between team members and utilizing other parts of your supply chain efficiently.
Continuous improvement is key to identifying bottlenecks and inefficiencies. Regularly reviewing and optimizing processes can help uncover areas for enhancement.
Here are some ways to improve OFCT:
- Promised Customer Order Cycle Time - This is the expected order fulfillment time you tell customers, and it's a good benchmark to keep track of other metrics.
- Actual Customer Order Cycle Time - This is the average time it takes for a customer to receive a product after ordering it, and it's what you should aim to reduce.
- Cash to Cash Cycle Time - This is the time taken from spending money on raw materials to receiving money from them as finished goods.
- Supply Chain Cycle Time - This is how long it takes to fulfill a customer order if the requisite raw materials are at zero.
By tracking and understanding these metrics, you can identify areas for improvement and make data-driven decisions to optimize your OFCT.
Outsource
Outsourcing your fulfillment can be a game-changer for your business. Red Stag Fulfillment uses Agile management practices to help your business grow and scale.
Outsourcing your fulfillment can help you lower your customer order cycle time. This means customers get their orders faster, which can lead to increased satisfaction and loyalty.
If your business is growing rapidly, outsourcing your inventory management to a 3PL like Red Stag can be a huge help. They can take care of storing, picking, and packing your products, freeing up your time to focus on other areas of your business.
A team of fulfillment fanatics at Red Stag care about their clients' businesses like their own. They see things from their customers' perspective, and have the guarantees to prove it.
Here are some benefits of outsourcing your fulfillment to a 3PL:
- Rapid fulfillment without sacrificing accuracy
- Expertise in inventory management and order fulfillment
- Guarantees to ensure your business grows without drag
Frequently Asked Questions
What is the duration of order fulfillment?
Order fulfillment cycle time, or OFCT, is the time it takes for customers to receive their purchases, directly impacting the customer experience. Shortening this time can be achieved by optimizing your supply chain and partnering with reliable shipping providers.
Featured Images: pexels.com